2D LiDAR vs 3D LiDAR: Which one is for me?
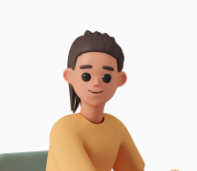
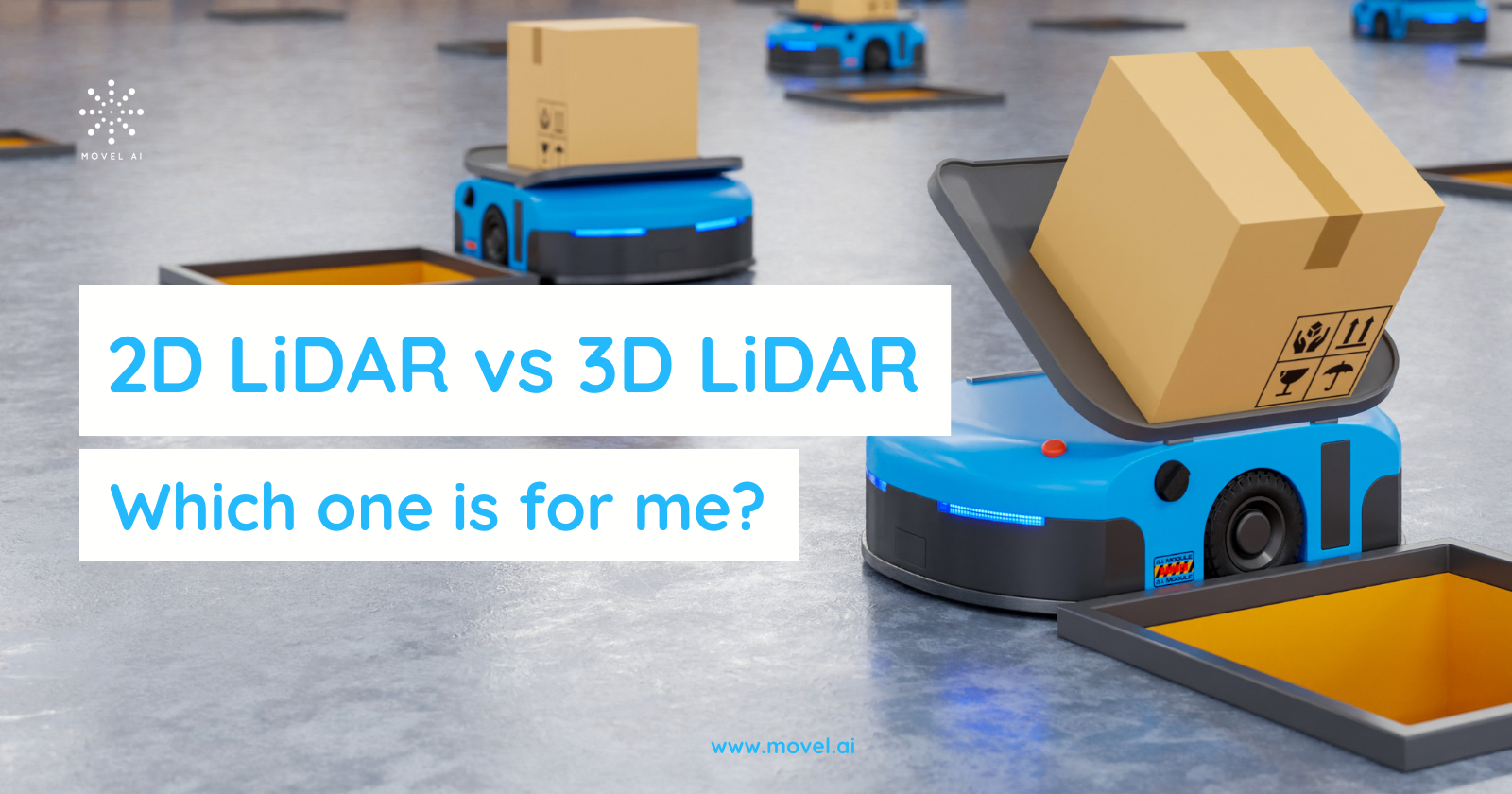
LiDAR stands for Light Detection and Ranging. According to Velodyne LiDAR, LiDAR technology uses eye-safe laser beams to “see” the world in 3D representation, providing machines and computers an accurate representation of the surveyed environment. LiDAR technology works very simply, emitting light to a target and measuring how long it takes to reflect back and return to the source. This process runs repeatedly, enabling the robots to see a 3D map of the surrounding area and navigate precisely.
LiDAR technology is often used in robotics, especially to navigate robots and enable it to work autonomously. By using 2D and 3D LiDAR technology, robots can see the environment as accurately as a human eye. Due to the artificial intelligence, robots will be able to move freely without worrying about colliding into nearby objects like walls, glasses, boxes, or other robots.
Difference between 2D LiDAR and 3D LiDAR
2D LiDAR emits a single beam to the targeted object on the horizontal axis. The sensor will then spin to collect X and Y coordinates. On the other hand, 3D LiDAR emits several beams on the vertical axis, to collect X, Y, and Z coordinates.
In summary, both 2D and 3D LiDAR work in the same way, they emit beams to let robots see. However, they have some significant differences.
Which LiDAR sensor is right for me?
Learning the difference between the two can make robotic manufacturers wonder which LiDAR sensor is right for their business. The answer is, it depends! Every business has a different type of robot to develop and budgets to deal with. Some have limited budgets, while others can go all out.
The environment in which the robots will operate is also essential to consider before deciding on the use of 2D or 3D LiDAR sensors. The problem with a pure 2D lidar based system is that it will fail when glass doors/windows are present or if the environment is dynamically changing. For example, in places such as warehouses, the production environment is constantly changing; or in a restaurant table positions change quite often with constant traffic of customer and staff which causes the robot to lose track of its positioning. 3D LiDAR can be used to resolve this issue, but they are more expensive.
Robotic navigation solution with 2D and 3D LiDAR
With this in mind, robot manufacturers have to choose between cost and performance, and then use them to build their robots. However, Movel AI has the solution for both the types of LiDARs, and answers the needs. The startup developed an AI-powered software platform that enables seamless robot navigation.
Movel AI offers a navigation solution with 2D and 3D LiDAR based simultaneously. By using a sensor-fusion based system, Movel AI is able to increase the accuracy to as low as 2cm, making it more accurate, compared to the industry standard of 5cm to 7cm.
Movel AI's technology, Seirios, eases the use of robotics with its easy to use interface and easy to deploy its solution on any kind of robot. Seirios can accelerate the robot's intelligence, enabling them to move freely without making your robot manager waste time navigating it. As a result, robot manufacturers can no longer worry about the development costs, since using this sensor with 3D capabilities will be more cost-effective.
Click here for a FREE 30-day no-obligation trial to see how your robot deployment can be easier!
Subscribe to my newsletter
Read articles from Macy directly inside your inbox. Subscribe to the newsletter, and don't miss out.
Written by
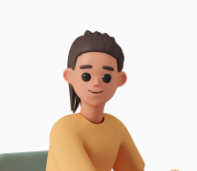