CAN Protocol

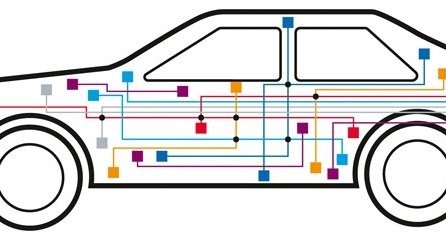
CAN (Controller Area Network) is a type of serial bus communication protocol used in automotive and industrial applications to connect electronic control units (ECUs). It is designed to be robust, highly reliable and capable of transmitting data between multiple nodes in a network with high speed and low latency. The protocol uses a message-based communication scheme where each node can send and receive messages in the form of frames. The frames contain the data being transmitted and an identifier that determines the priority of the message. The CAN protocol also includes error detection and correction mechanisms to ensure the integrity of the data being transmitted.
The Controller Area Network (CAN) protocol is a communication standard used in vehicles and industrial automation systems to control and monitor various devices. It was designed to be a cost-effective, high-speed, and reliable solution for communication between microcontrollers, sensors, and actuators.
Some key features of the CAN protocol include:
Broadcast communication: All nodes on the network receive data transmitted by any other node.
Multi-master capability: Multiple nodes can transmit data at the same time.
Prioritized communication: CAN assign a priority to each message, ensuring that important messages are transmitted first.
Error detection: CAN include mechanisms for detecting errors in data transmission, such as checksum and cyclic redundancy check (CRC).
Robustness: CAN is designed to operate in harsh environments, and can tolerate electrical noise and other disturbances.
The CAN protocol is used in various applications, including automotive, aerospace, industrial automation, and medical devices. There are two standard versions of the CAN protocol: CAN 2.0A and CAN 2.0B. The main difference between the two is that CAN 2.0B includes an improved method for error detection.
Wiring Diagram of CAN Protocol:
The wiring diagram of a CAN network is relatively simple and typically consists of two wires: CAN High (CAN_H) and CAN Low (CAN_L).
The CAN_H and CAN_L wires are connected to a transceiver in each device that is connected to the network. The transceiver is responsible for converting digital signals from the device into differential voltage signals that are transmitted over the CAN_H and CAN_L wires.
In a typical CAN network, the CAN_H and CAN_L wires are connected in a twisted-pair configuration to minimize electrical noise. A termination resistor is also connected at each end of the network to prevent signal reflections.
Each device connected to the network is also assigned a unique identifier, called a CAN node ID, which is used to identify the source of the data being transmitted.
Here's a simple example of a CAN wiring diagram:
+-----+ +-----+ +-----+
|Node1|---|Node2|---|Node3|
+-----+ +-----+ +-----+
| Transceiver | Transceiver | Transceiver |
+-------------+-------------+-------------+
| CAN_H | CAN_H | CAN_H |
| CAN_L | CAN_L | CAN_L |
+-------------+-------------+-------------+
| | |
Termination Termination Termination
Resistor Resistor Resistor
This is a simple example and actual CAN network wiring diagrams can be much more complex depending on the number of nodes, the distance between nodes, and the presence of other electrical devices that can interfere with the signals.
A CAN protocol timing diagram is a graphical representation of the timing relationships between different signals in a CAN network. It provides a visual representation of the time required to transmit data, the time between frames, and the error detection and signalling mechanisms used in CAN.
Here's a simple example of a CAN protocol Timing Diagram:
____________
| SOF |
----------
| Identifier|
----------
| RTR |
----------
| DLC |
----------
| Data |
----------
| CRC |
----------
| ACK Slot |
----------
| ACK Delim|
----------
| End of Frame |
----------
In this diagram, the Start of Frame (SOF) signal marks the start of a new data frame. The Identifier field contains the unique identifier of the transmitting node, while the Remote Transmission Request (RTR) field indicates whether the frame is a data frame or a remote frame. The Data Length Code (DLC) field indicates the number of bytes of data in the frame. The Data field contains the payload data, while the Cyclic Redundancy Check (CRC) field is used for error detection. The ACK Slot is a time slot reserved for the receiving node to send an acknowledge signal, and the ACK Delimiter signal marks the end of the ACK slot. The End of Frame signal marks the end of the data frame.
There are two main types of CAN (Controller Area Network) protocols: standard CAN (also known as classical CAN) and extended CAN.
Standard CAN: Standard CAN is the original CAN specification and is used in most automotive and industrial applications. It uses an 11-bit identifier and supports a maximum data rate of 1 Mbps. Standard CAN is suitable for small and simple networks where the priority of messages is not critical.
Extended CAN: Extended CAN also be known as CAN 2.0B, is an extended version of the standard CAN specification. It uses a 29-bit identifier and supports a maximum data rate of 1 Mbps. Extended CAN is used in complex networks where higher-priority messages need to be transmitted before lower-priority messages.
Both types of CAN protocols use a differential voltage signalling method to transmit data and use the same basic frame structure, but the extended CAN protocol provides a much larger address space and is therefore better suited for complex networks with many nodes.
In summary, the choice of CAN protocol depends on the requirements of the specific application. Standard CAN is usually sufficient for small networks with simple communication requirements, while extended CAN is better for larger and more complex networks.
Applications of CAN Protocol:
Automotive: CAN protocol is widely used in automotive systems for communication between different ECUs (Electronic Control Units) in a vehicle, such as an engine control, transmission control, and ABS control.
Industrial Control: CAN is used in industrial control systems for communication between different devices, such as PLCs (Programmable Logic Controllers), sensors, and actuators.
Medical Devices: CAN is used in medical devices such as patient monitors, infusion pumps, and dialysis machines for communication between different components.
Aerospace: CAN is used in aerospace systems for communication between different systems, such as avionics and navigation systems.
Merits of CAN Protocol:
Reliability: CAN uses a robust differential voltage signalling method and provides mechanisms for error detection and correction, making it a highly reliable communication protocol.
Ease of Use: CAN is a simple and easy-to-use protocol with a standard message format and a large address space, making it suitable for a wide range of applications.
High Speed: CAN supports data rates up to 1 Mbps, making it suitable for high-speed applications.
Cost-effective: CAN is a cost-effective protocol that uses simple and inexpensive components, making it suitable for a wide range of applications.
Demerits of CAN Protocol:
Limited Data Rate: Although CAN supports data rates up to 1 Mbps, this may not be sufficient for some high-speed applications.
Limited Address Space: The standard CAN protocol uses an 11-bit identifier, which may not be sufficient for large and complex networks with many nodes.
Complexity: CAN can be a complex protocol, requiring specialized knowledge and experience to design and implement it effectively.
In conclusion, CAN protocol is widely used in a variety of applications due to its reliability, ease of use, and cost-effectiveness. However, its limited data rate and address space, and complexity can be limiting factors in some applications.
Subscribe to my newsletter
Read articles from Mithilesh Gaikwad directly inside your inbox. Subscribe to the newsletter, and don't miss out.
Written by

Mithilesh Gaikwad
Mithilesh Gaikwad
Hi there! My name is Mithilesh Gaikwad and I am a Embedded System Developer with a year of experience in the industry, specializing in the Microcontroller and OS System programming. I am currently employed at CDAC, where I have had the opportunity to work on a variety of projects using the Vega Processor, STM32, Linux Distros specially in Software Development.