17 glossary terms that an industrial automation engineer must know
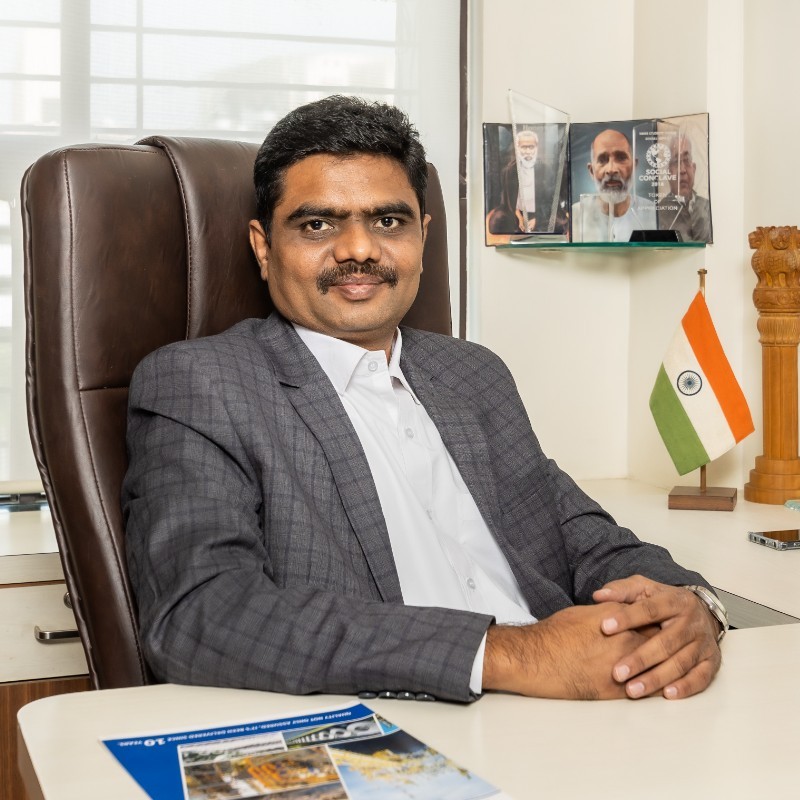
Industrial automation engineers work with complex systems to improve efficiency, productivity, and safety in manufacturing and production processes. Here are some important glossary terms they should be familiar with:
Actuators - Devices that control physical processes or systems based on instructions from automation systems. Examples include motors, valves, and solenoids.
Controllers - Manage and coordinate devices to automate a process. They receive inputs, process information, and generate outputs to control actuators or devices.
Distributed Control System (DCS) - An industrial automation system used for monitoring and controlling processes in manufacturing and production.
Human-Machine Interface (HMI) - The interface between humans and automation systems, typically through graphical user interfaces, that allow operators to monitor and control automated processes.
Industrial Internet of Things (IIoT) - The use of internet-connected devices, sensors, and data analytics in industrial automation to enable remote monitoring, diagnostics, and optimization of processes and systems.
Machine Vision - The use of computer vision technology in automation to capture, analyze, and interpret visual information for tasks like inspection, measurement, identification, and guidance.
Motion Control - The management of machinery movement using techniques like servo motors, actuators, drives, and controllers.
Personal Protective Equipment (PPE) - Specialized gear or clothing worn to protect individuals from workplace hazards. Proper use and maintenance of PPE are crucial for ensuring worker safety.
Programmable Logic Controller (PLC) - A specialized type of computer that is used to control and automate industrial processes. PLCs are designed for reliability, durability, and real-time control.
Sensors - Devices that detect and measure physical or chemical parameters, such as temperature, pressure, humidity, flow, or position, and provide feedback to automation systems for control and monitoring purposes.
Servo Controls - Hardware and software components that ensure accurate and smooth motion control. They are commonly used in robotics and CNC machines.
Variable Frequency Drive (VFD) - An electronic device used to control the speed and torque of electric motors in automation and industrial applications by varying the frequency and voltage of the input power.
Communication Protocols - Set of rules governing how devices communicate. Examples include Profibus, Ethernet/IP, Modbus, and OPC UA.
Control Algorithms - Mathematical algorithms or logic used in automation systems to process data, make decisions, and generate control signals.
Noise Rejection - The ability to filter out unwanted interference from signals through techniques like shielding, filtering, and signal processing.
Process Control - A systematic management and regulation of industrial processes using sensors, controllers, and feedback loops to adjust process parameters in real-time.
Safety Systems - Systems designed to ensure the safety of operators, equipment, and processes in automation systems.
Further resources:
Subscribe to my newsletter
Read articles from Waman Sanap directly inside your inbox. Subscribe to the newsletter, and don't miss out.
Written by
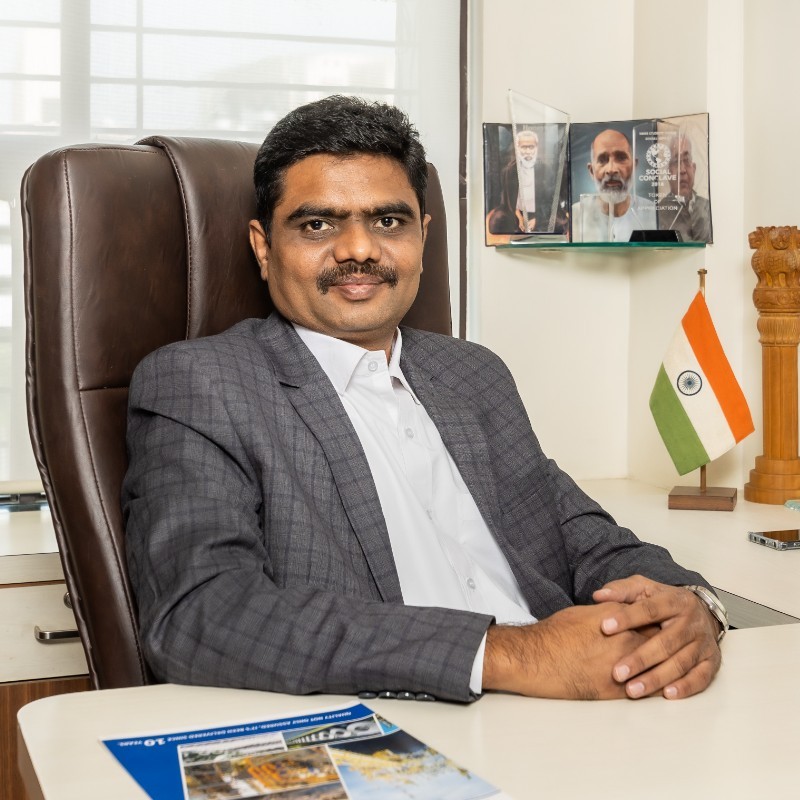
Waman Sanap
Waman Sanap
Waman Sanap, the Chief Executive Officer at iPAC Automation Pvt. Ltd., is a visionary leader with over 15 years of full-time experience in the instrumentation and control automation engineering field. As the founder and director of iPAC Automation, he initiated the company's journey in 2008 with a small team providing automation services on Honeywell TPS and DCS platforms, as well as instrumentation detailing and designing. Under his guidance, iPAC Automation has grown into a major service provider, executing over 100 projects across domains such as Oil & Gas, Refinery, Power Plant, and Pharmaceuticals worldwide. With a mission to be a preferred service partner to EPC companies, iPAC Automation specializes in a wide range of services, including field instrumentation and electrical detailing, SPI Intools, migration projects, reverse engineering, DCS and PLC system implementation, and more.