Industrial Internet of Things (IIOT)

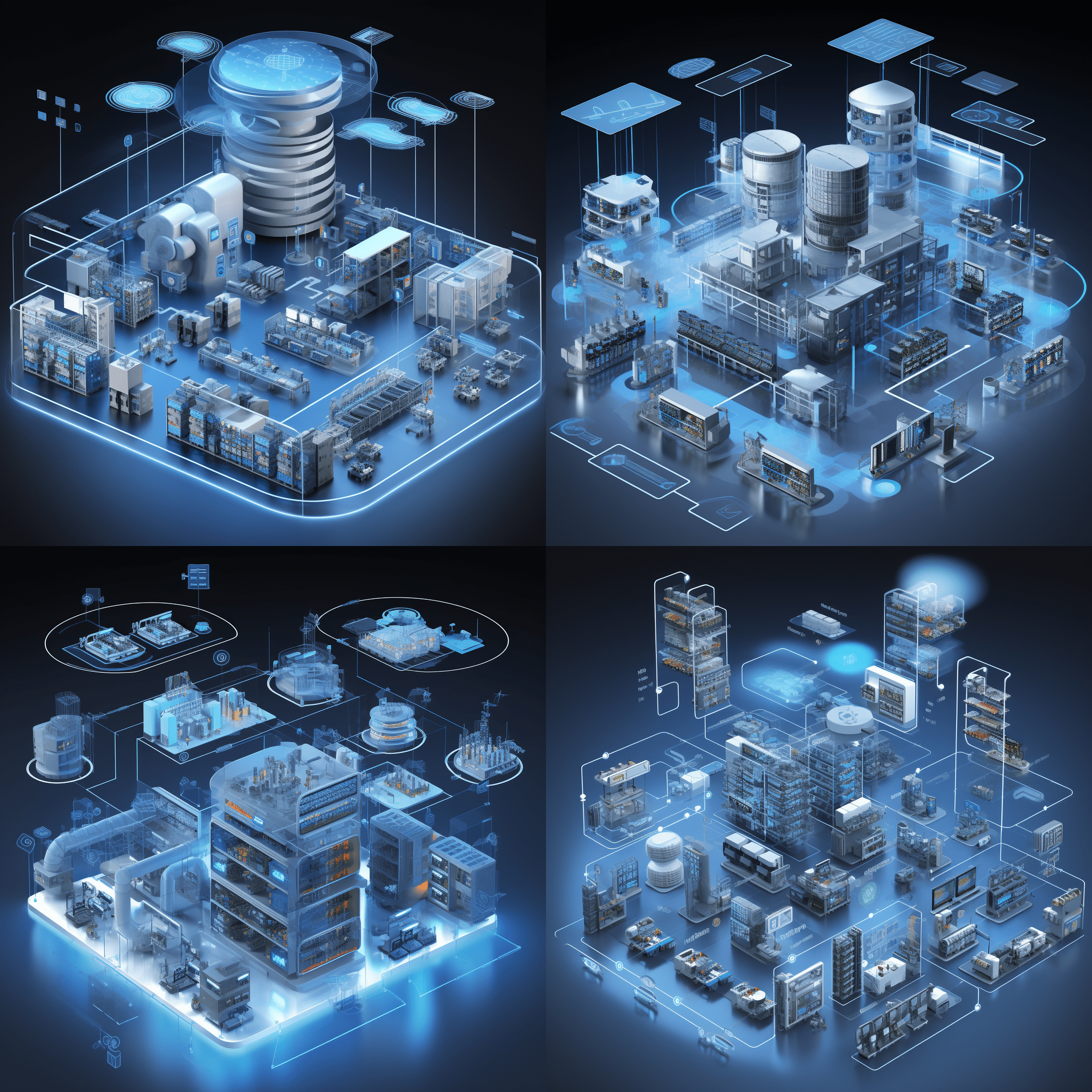
In this blog , We'll try to grasp what Industrial Iot is and why we need ?. I'll do my best to explain it and its objectives. In the era of Industry 4.0, the Industrial Internet of Things (IIOT) has emerged as a transformative force, reshaping the landscape of industrial automation.
Before IIOT:
The Evolution of Automation Layers:
Layer 0: Field Devices and Instruments:
- Collects raw data from the production environment.
Layer 1: Control Systems:
- Processes data to manage and optimize industrial processes.
Layer 2: Supervisory Control:
- Provides real-time oversight for monitoring and control.
Layer 3: Manufacturing Operations Management (MOM):
- Optimizes overall manufacturing operations, bridging shop floor and enterprise level.
Layer 4: Enterprise Resource Planning (ERP):
- Integrates various business operations, including finance and supply chain management.
The evolution of industrial automation, the connection between each layer forms a cohesive and integrated framework, ensuring the efficient flow of information and control. Let's explore how these layers connect:
Layer 0 to Layer 1 (Field Devices to Control Systems):
Field devices and instruments collect raw data from the production environment.
Control systems, including PLCs and DCS, process this data to manage and optimize industrial processes.
The connection is established through communication protocols, ensuring a smooth transfer of data for real-time control.
Layer 1 to Layer 2 (Control Systems to Supervisory Control):
Processed data from control systems is sent to supervisory control systems.
Supervisory control adds a higher level of oversight, allowing operators to monitor and control various processes in real-time.
Communication channels, often through networked systems, enable seamless interaction between these layers, providing immediate insights to operators.
Layer 2 to Layer 3 (Supervisory Control to Manufacturing Operations Management - MOM):
Data from supervisory control systems is integrated into MOM systems.
MOM focuses on optimizing overall manufacturing operations, bridging the gap between the shop floor and the enterprise level.
Communication interfaces, such as APIs or middleware, facilitate the exchange of data between supervisory control and MOM, ensuring a unified approach to production optimization.
Layer 3 to Layer 4 (Manufacturing Operations Management to Enterprise Resource Planning - ERP):
MOM systems contribute data to ERP systems, integrating manufacturing operations with broader business functions.
ERP systems, managing finance, human resources, and supply chain, rely on real-time information from MOM for comprehensive decision-making.
Integration platforms and standardized data formats enable a seamless connection between the manufacturing operations on the shop floor and the overarching business strategy.
The problem here with traditional automation process:
This lack of flow of real-time data between different layers, hindering the ability to make informed decisions.
Data generated by field devices and instruments in traditional automation is often stored in isolated databases or systems. This fragmentation makes it challenging to derive meaningful insights across the entire manufacturing process.
Human intervention, traditional pen and paper is used for collecting data at few layers etc...
Maintenance issues etc...
Summary
Industrial IoT (IIoT) has the potential to revolutionize industries by enabling automation and increasing efficiency. By connecting various devices and systems, IIoT allows for real-time monitoring, data analysis, and predictive maintenance, leading to improved operational efficiency and reduced downtime.
Understanding IIOT
As discussed earlier , Traditional integration involves connecting devices and systems through hard-wired connections, which can be time-consuming and costly. In contrast, At its core, IIoT involves the integration of smart devices, sensors, and machinery within industrial processes, all interconnected through the internet. This interconnected network enables the seamless exchange of data, fostering improved decision-making, increased efficiency, and enhanced operational capabilities.
IIoT leverages wireless connectivity and cloud-based infrastructure, promoting faster, more flexible integration and enabling remote management and control. Within this framework, the MQTT (Message Queuing Telemetry Transport) protocol plays a pivotal role. Operating on a publish-subscribe model, MQTT facilitates seamless communication across different layers of the IIoT architecture.
Case Study:
Predictive Maintenance in Manufacturing:
Problem: A leading manufacturing plant faced frequent equipment breakdowns, causing production delays.
Solution: Implemented IIoT sensors to monitor equipment health in real-time. Outcome: Predictive maintenance reduced downtime by 40%, leading to significant cost savings.
Smart Agriculture for Crop Monitoring:
Problem: Agricultural inefficiencies and resource wastage due to outdated practices.
Solution: Deploy IIoT-enabled sensors to monitor soil moisture, temperature, and crop health.
Outcome: Precision farming resulted in a 20% increase in crop yield and a 30% reduction in water usage.
Energy Management in Utilities:
Problem: High energy consumption without a clear understanding of usage patterns.
Solution: Integrated IIoT devices to monitor energy consumption in real-time. Outcome: Optimized energy usage, leading to a 15% reduction in energy costs and improved sustainability.
what a cloud can do in IIoT:
The cloud layer in IIoT (Industrial Internet of Things) plays a pivotal role in enhancing the capabilities and functionalities of industrial automation. Here are several key aspects of what a cloud layer can do in IIoT:
Data Storage and Management:
- The cloud provides vast and scalable storage for the enormous volumes of data generated by IIoT devices. It allows industries to efficiently store, organize, and manage data from various sources, enabling historical analysis and long-term insights.
Real-Time Data Processing:
- Cloud platforms offer powerful computing resources that facilitate real-time data processing. IIoT devices can transmit data to the cloud, where it can be processed, analyzed, and transformed into actionable insights promptly. This real-time capability is crucial for making informed decisions on the fly.
Advanced Analytics and Machine Learning:
- Cloud-based analytics and machine learning services enable industries to derive meaningful patterns and predictions from the vast amounts of data collected through IIoT. This allows for predictive maintenance, process optimization, and the identification of trends that might not be apparent through traditional analysis methods.
Remote Monitoring and Control:
- The cloud enables remote monitoring and control of industrial processes. This means that operators and decision-makers can access real-time data, monitor equipment status, and even control processes from anywhere with an internet connection. This remote accessibility enhances operational flexibility and responsiveness.
Scalability:
- Cloud services are inherently scalable, allowing industries to expand their IIoT implementations without the need for significant upfront investments in infrastructure. This scalability is essential as industrial operations grow, and more devices are added to the IIoT ecosystem.
Cybersecurity and Authentication:
- Cloud providers implement robust cybersecurity measures to protect IIoT data during transmission and storage. Features like encryption, secure authentication, and access controls are integrated into cloud platforms to ensure the confidentiality and integrity of sensitive industrial data.
Collaboration and Integration:
- Cloud platforms facilitate collaboration and integration by providing a centralized environment where data from various sources can be aggregated. This enables different departments, suppliers, and stakeholders to access relevant information, fostering better collaboration across the supply chain.
Conclusion: The Industrial Internet of Things is more than just a technological advancement; it's a catalyst for profound changes in how industries operate. The case studies presented here are just a glimpse of the transformative potential of IIoT. As industries continue to embrace this revolution, the benefits of increased efficiency, cost savings, and improved safety will undoubtedly drive further innovation and adoption. Stay tuned for more in-depth explorations of specific aspects of IIoT in our upcoming blog posts.
Subscribe to my newsletter
Read articles from THARUN directly inside your inbox. Subscribe to the newsletter, and don't miss out.
Written by