Synergizing Supply Chains: A Hybrid Metaheuristic Framework for Efficient Automotive Parts Delivery with Customer Clustering
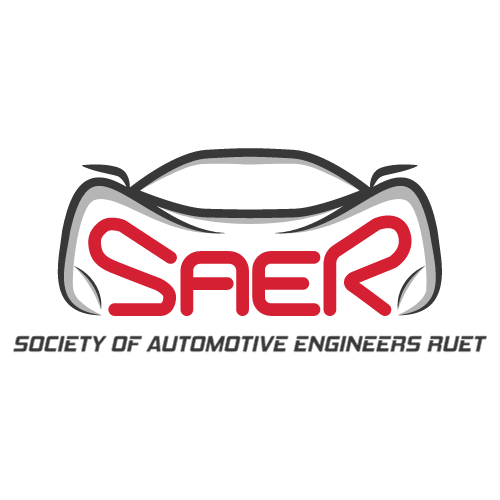
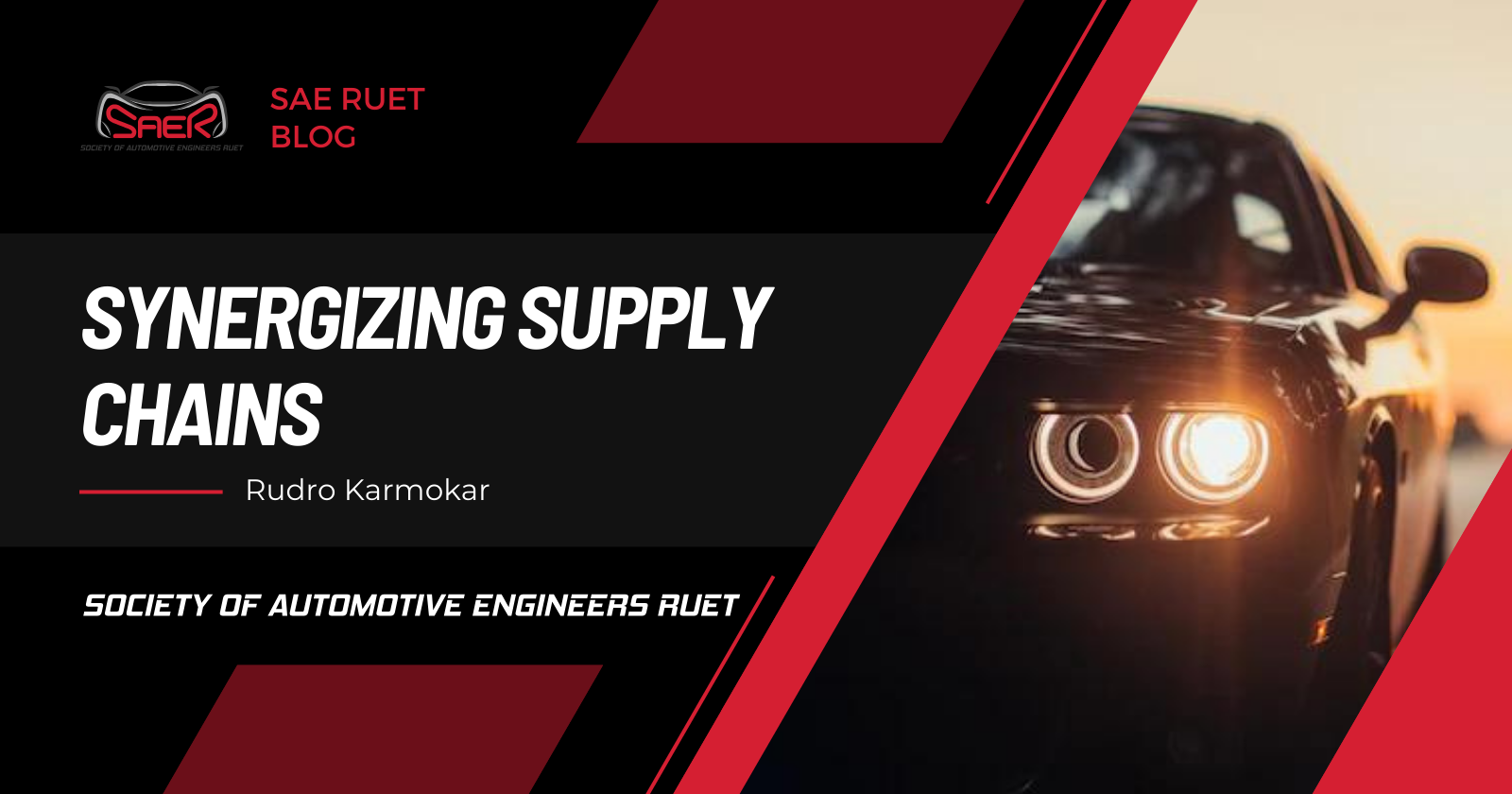
Through the integration of a hybrid metaheuristic & the introduction of customer clustering, the framework can play an important role in revolutionizing automotive parts delivery, contributing to increased efficiency, reduced costs, and an upgraded level of service in the automotive supply chain.
The developments of globalization have enabled the business scope of companies to expand continuously. To keep up with the pace of globalization and develop an enterprise scale rapidly, leaders have paid more attention to the role of logistics. Reasonable and rigorous transportation route scheduling not only reduces logistics costs but also improves customers’ satisfaction. The problem of route scheduling is called a vehicle routing problem (VRP), which is a classical combinatorial optimization problem. In a VRP, there are customers each having different demands. A depot provides services to customers by organizing efficient transportation routes. Under certain constraints, the goal is to satisfy the demands of all customers and seek the shortest route distance simultaneously. In recent years, with the improvement of living standards, automobile consumption has become more widespread. The increasing sales make a number of automobile companies fiercely compete. It is well known that more than 3000 parts are needed for assembling an automobile, which makes the company cost more in transferring parts from multiple parts manufacturers. Different from traditional VRP, demand distribution is relatively scattered and irregular. By analyzing existing VRP variants, there are two types of VRPs with clustering features, which are the clustered vehicle routing problem (CluVRP) and the generalized vehicle routing problem (GVRP). The original prototype of both models is the classical capacitated vehicle routing problem (CVRP) with load constraints. The most widely used clustering principle is geographical proximity. In the CluVRP, customers belonging to the same cluster must be serviced by the same vehicle. When the vehicle leaves a cluster, it must have served all customers in the cluster according to a scheduled sequence. This is a hard constraint. After that, the vehicle can continue to serve another cluster or return to the depot. The other model with clustering features is the GVRP. It is characterized by the fact that a vehicle serves only one customer within a cluster according to the schedule, and other customers will be ignored. The difference between the two problems is that all customers or one customer must be served in each cluster. Now the question comes: Why does the CluVRP play an important role in enterprise logistics? To answer it with automotive parts delivering with customer clustering is that it will give maximum efficiency. Because vehicles only run one delivery with the least amount of time. Therefore, the route schedulers prefer to arrange vehicles to serve customers that belong to the same area. From the perspective of the logistics company, the distribution costs are reduced, and the effective compactness of the route is increased. From the perspective of the drivers, it is conducive to increasing familiarity with the route and to speeding up the delivery. Another topic is that the resources are limited. Social development has led to increasing logistical requirements day by day, but only limited resources, including human and material resources are available, which often lead to service providers being unable to meet all needs. It is a good way to differentiate customers into multiple subranges and to allow multiple service providers to arrange service in a timely manner. In addition to these scenarios, there are also other meaningful scenarios in which the CluVRP can play a valuable role.
The trend of clustering in automobile parts suppliers is gradually obvious. As analyzed above, the related transportation problem can be classified as a CluVRP problem. The overall optimal solution was obtained by merging the inter-cluster route and intra-cluster route results. To balance exploration and exploitation of VNS-LKDP, the results also need to be augmented with a diversity control operation, which consists of a perturbation operator and a repair operator. Disturbing customers by a perturbation operation may destroy the integrity of the cluster. Due to the hard constraint, a vehicle has to finish servicing all customers in the same cluster before moving to the next cluster. If the perturbation operation occurs at the customer level, it may lead to some customers being removed from their formed clusters, the integrity of the original cluster would be destroyed, which is contrary to the hard constraint. Therefore, the perturbation was carried out only at the cluster level, and customer order in each cluster remained unchanged.
At last, we discussed the CluVRP problem derived from logistics companies, which is a new variant of classical CVRP. The demand distribution of CVRP is scattered and irregular, but CluVRP has its particular hard constraint: the geographical location of parts manufacturers had already presented clustering distribution before planning the route schedule and all customers in a cluster have to be served consecutively by the same vehicle. The CluVRP seems to be more in line with the current route planning scenario in the world.
Subscribe to my newsletter
Read articles from Society of Automotive Engineers RUET directly inside your inbox. Subscribe to the newsletter, and don't miss out.
Written by
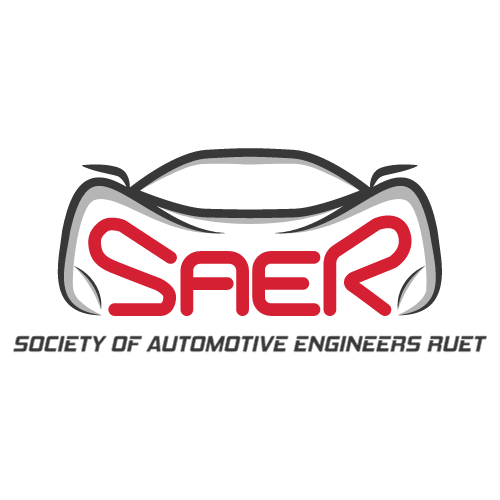
Society of Automotive Engineers RUET
Society of Automotive Engineers RUET
SAER, an educational organization, is committed to fostering a passion for engineering among RUET students. Its focus extends to the dynamic realms of automotive, aerospace, and commercial vehicles.