Distillation: A Chemical Engineer's Toolkit for Separation

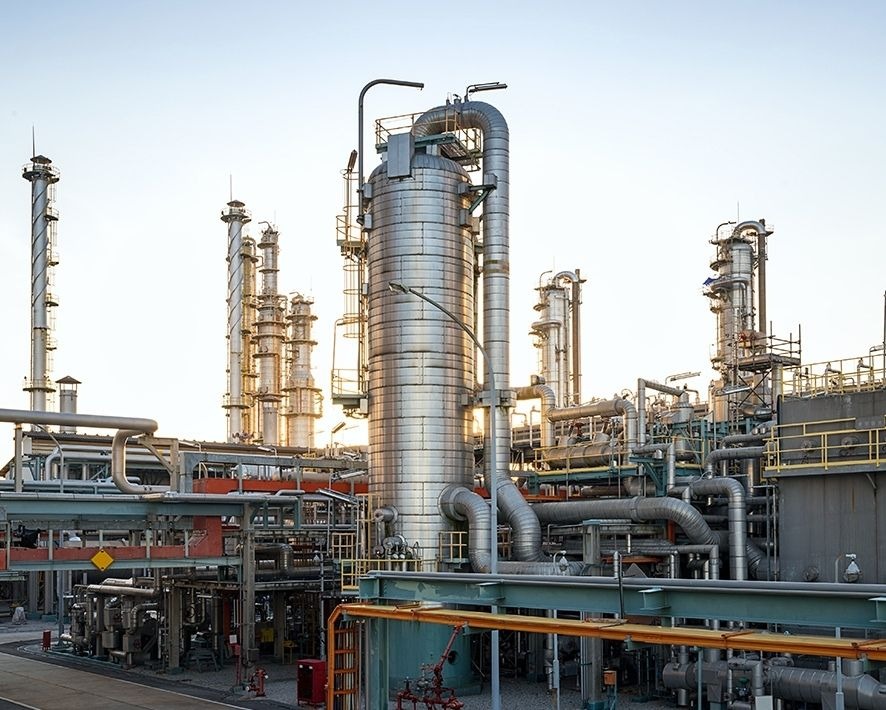
Distillation is the unit operation which is used in a chemical industry to separate
mixed liquid or components based on there boiling points.
The Essence of Distillation: Boiling Point Ballet
At its core, distillation is a simple yet powerful technique for separating components in a mixture based on their boiling points. Imagine a mixture of two liquids, like water and alcohol (ethanol). Each component has a specific boiling point – the temperature at which it transitions from liquid to vapor. In distillation, we heat the mixture:
The lower-boiling-point component (ethanol) vaporizes first.
This vapor is then captured and cooled in a condenser, transforming it back into liquid form – our desired product, or distillate.
The remaining liquid, enriched in the higher-boiling-point component (water), is called the bottoms.
Beyond the Basics: A Spectrum of Distillation Techniques
Distillation's versatility lies in its adaptability. By manipulating temperature, pressure, and even the design of the distillation column, engineers can achieve remarkable feats of separation:
Fractional Distillation: For mixtures with more than two components or components with very close boiling points, we employ fractional distillation. Imagine a series of stacked distillation columns, each enriching the product stream in a specific component. This is how crude oil is separated into various fractions like gasoline, diesel, and jet fuel.
Azeotropic Distillation: But what happens when the components in a mixture form an azeotrope – a constant boiling liquid mixture? Simple distillation won't achieve complete separation. Chemical engineers employ specialized techniques like azeotropic distillation, where a third component is added to alter the relative volatilities and enable separation.
Continuous Distillation: The world of distillation doesn't stop at batch processes. Continuous distillation allows for uninterrupted processing, making it ideal for large-scale industrial applications. These sophisticated columns continuously feed the mixture and withdraw products, maximizing efficiency and production output.
Distillation's Impact: From Biofuels to Pharmaceuticals
Distillation's influence extends far beyond the beverage industry. Here are some fascinating applications:
Desalination: Distillation plays a vital role in desalination, the process of removing salt from seawater. By heating seawater and condensing the vapor, we obtain fresh, drinkable water – a critical technology for regions with limited access to freshwater sources.
Biofuels on the Rise: Biofuels, a promising alternative to fossil fuels, rely on distillation for their production. Processes like ethanol distillation from fermented plant matter utilize this technique to separate the desired biofuel from the fermentation broth.
Pharmaceutical Purification: Distillation plays a crucial role in purifying valuable pharmaceutical products. By carefully controlling the distillation process, engineers can isolate and purify medications with high precision.
The Future of Distillation: Innovation and Sustainability
As the world strives for sustainability and resource efficiency, the future of distillation looks bright. Here are some exciting trends:
Membrane Distillation: This emerging technology utilizes membranes to selectively allow the passage of vapor, offering potential for energy-efficient distillation processes.
Vacuum Distillation: By reducing the pressure in the distillation column, the boiling point of components is lowered. This can be beneficial for heat-sensitive materials.
Steps to design distillation column
Distillation remains a cornerstone of chemical engineering, its simplicity masking its remarkable versatility. From the water we drink to the lifesaving drugs we rely on, distillation plays a vital role in separating the essential components that shape our world. So, the next time you raise a glass or quench your thirst, remember the silent magic of distillation working tirelessly behind the scenes!
Distillation columns, the workhorses of separation in the chemical engineering world, require meticulous design to achieve optimal performance. Here's a breakdown of the key steps involved in designing a distillation column:
1. Define Separation Objectives:
Product Composition: Specify the desired purity of your product (distillate) and the maximum allowable concentration of impurities.
Recovery: Determine the target percentage of the desired component you want to recover from the feed mixture.
2. Understand Your Mixture:
Components: Identify all the components present in the feed mixture and their relative volatilities (boiling point differences).
Feed Properties: Gather data on the composition, flowrate, and physical properties (boiling point, viscosity) of the feed mixture.
3. Choose the Operating Pressure:
Pressure impacts volatility: Higher pressure increases boiling points, affecting the ease of separation.
Economics and Equipment: Consider the cost and limitations of pressure vessels as pressure increases.
Energy Consumption: Lower pressure distillation might require more energy due to higher vapor volumes.
4. Minimum Reflux Ratio (Rmin) and Minimum Number of Stages (Nmin):
Rmin: This ratio defines the minimum amount of reflux (distillate returned to the column) needed for desired separation.
Nmin: The minimum number of theoretical equilibrium stages required within the column for effective separation.
Shortcut Methods: Software tools or shortcut methods like McCabe-Thiele or Ponchon-Savarit are used to estimate Rmin and Nmin.
5. Column Diameter and Height:
Diameter: This is influenced by vapor and liquid flow rates within the column.
Height: The number of theoretical stages (N) translates to the actual height of the column packing or trays.
Packing or Trays: Choose between packing material (randomly placed elements) or trays (horizontal plates) for internal column design. Each offers advantages for different applications.
6. Additional Considerations:
Feed Stage Location: The optimal location within the column to introduce the feed mixture can significantly impact separation efficiency.
Entrainment and Flooding: Design considerations need to prevent excessive liquid droplets being carried upwards by the vapor stream (entrainment) or excessive liquid backup on trays (flooding).
Heat Exchangers: Reboiler and condenser design is crucial for efficient heat transfer and energy consumption optimization.
Remember: Distillation column design is often an iterative process. Initial estimates might be refined based on simulation tools or pilot plant testing to ensure the final design meets all performance and economic objectives.
Beyond the Steps: Software and Expertise
Chemical engineers leverage specialized software tools to model and simulate distillation column performance. These tools help evaluate different design options and predict separation efficiency, pressure drop, and energy requirements.
However, the expertise of a chemical engineer remains crucial. Understanding the underlying principles, selecting the appropriate design methods, and interpreting simulation results are essential for translating theory into a practical and efficient distillation column design.
By following these steps and leveraging the power of software tools, chemical engineers can design distillation columns that achieve exceptional separation performance, optimize resource utilization, and meet the ever-evolving demands of the process industry.
Subscribe to my newsletter
Read articles from Anand Rode directly inside your inbox. Subscribe to the newsletter, and don't miss out.
Written by
