Industry 4.0: The Future of Manufacturing
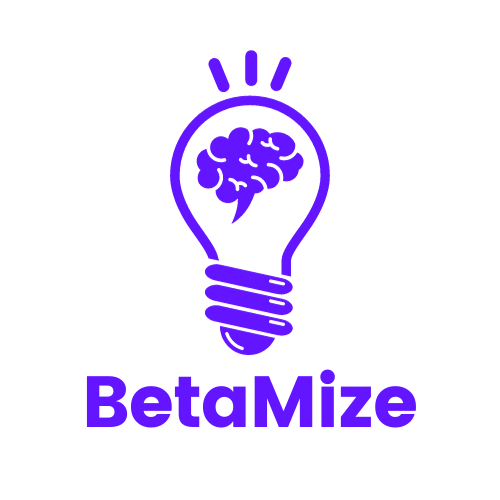
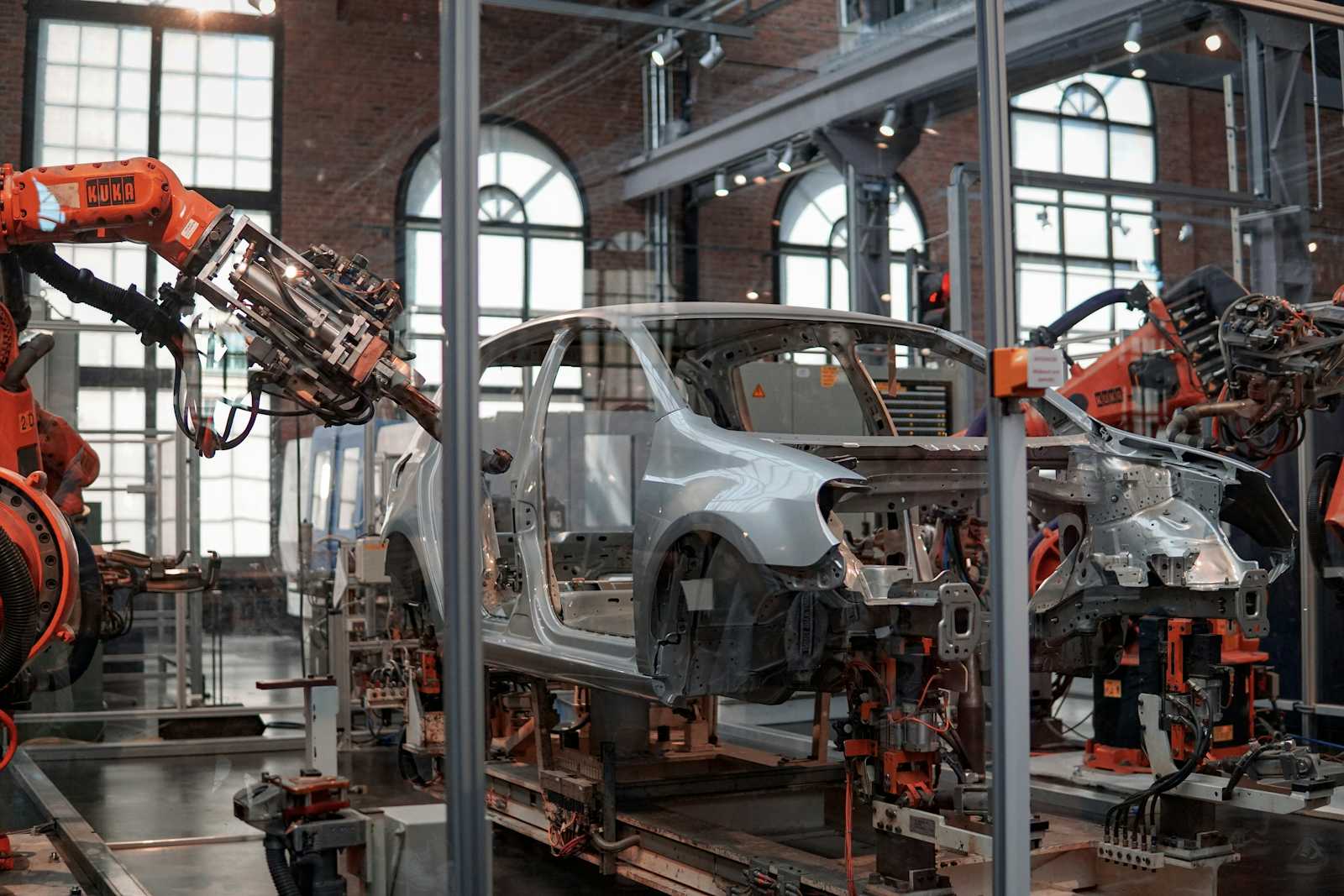
The manufacturing landscape is undergoing a significant transformation, driven by the advent of Industry 4.0. This new era, characterized by the fusion of advanced technologies, is revolutionizing the way we produce goods, enhance operational efficiency, and respond to market demands. In this blog post, we'll explore what Industry 4.0 entails, the challenges it addresses, and how businesses can leverage it to stay competitive in the modern manufacturing environment.
What is Industry 4.0?
Industry 4.0, also known as the Fourth Industrial Revolution, refers to the integration of digital technologies into manufacturing processes. It encompasses a range of advanced technologies including the Internet of Things (IoT), artificial intelligence (AI), machine learning, robotics, big data analytics, and cloud computing. These technologies work together to create smart factories where machines and systems communicate and collaborate in real-time.
Key Components of Industry 4.0
Internet of Things (IoT):
- IoT enables machines, devices, and sensors to connect and exchange data, providing real-time insights into production processes and equipment performance.
Artificial Intelligence and Machine Learning:
- AI and machine learning algorithms analyze vast amounts of data to optimize operations, predict maintenance needs, and enhance decision-making.
Big Data Analytics:
- Big data analytics involves processing and analyzing large datasets to uncover patterns, trends, and insights that drive operational improvements and strategic decisions.
Robotics and Automation:
- Advanced robotics and automation streamline production processes, reduce human error, and increase efficiency and precision in manufacturing.
Cloud Computing:
- Cloud computing provides scalable and flexible computing resources, enabling real-time data access, storage, and processing across the organization.
Cyber-Physical Systems (CPS):
- CPS integrates physical processes with digital systems, allowing for seamless interaction and coordination between machinery and computer-based algorithms.
Challenges Addressed by Industry 4.0
Operational Inefficiencies:
- Traditional manufacturing processes often suffer from inefficiencies due to manual operations, outdated equipment, and lack of real-time data. Industry 4.0 technologies enable real-time monitoring, predictive maintenance, and automation, significantly improving operational efficiency.
Supply Chain Disruptions:
- Disruptions in the supply chain, such as delays, shortages, and demand fluctuations, can impact production schedules and profitability. Industry 4.0 enhances supply chain visibility, enabling better demand forecasting, inventory management, and supplier collaboration.
Quality Control and Assurance:
- Maintaining consistent product quality is a persistent challenge. Industry 4.0 solutions utilize AI, machine learning, and IoT to monitor production quality in real-time, identify defects early, and implement corrective actions promptly.
Workforce Skill Gaps:
- The shift towards digital manufacturing requires a workforce skilled in advanced technologies. Industry 4.0 promotes workforce development through training programs, augmented reality (AR) for maintenance and repair, and AI-driven assistance systems.
How Businesses Can Leverage Industry 4.0
Invest in Smart Technologies:
- Adopting IoT, AI, robotics, and cloud computing can transform traditional manufacturing processes into smart, data-driven operations. Businesses should invest in these technologies to enhance efficiency, reduce costs, and improve product quality.
Data-Driven Decision Making:
- Leveraging big data analytics allows manufacturers to make informed decisions based on real-time insights. This data-driven approach helps optimize production schedules, reduce downtime, and respond to market changes swiftly.
Enhance Collaboration and Integration:
- Industry 4.0 promotes seamless integration and collaboration across the entire value chain. Businesses should focus on integrating their supply chain, production, and distribution processes to achieve greater transparency and efficiency.
Prioritize Cybersecurity:
- With increased connectivity comes the risk of cyber threats. Implementing robust cybersecurity measures is crucial to protect sensitive data and ensure the integrity of manufacturing operations.
Foster a Culture of Innovation:
- Embracing Industry 4.0 requires a cultural shift towards innovation and continuous improvement. Businesses should encourage experimentation, invest in employee training, and stay abreast of emerging technologies and industry trends.
The Future of Manufacturing with Industry 4.0
Industry 4.0 is not just a trend; it is the future of manufacturing. By integrating advanced technologies, businesses can achieve unprecedented levels of efficiency, agility, and competitiveness. The transition to Industry 4.0 may seem daunting, but the long-term benefits far outweigh the initial challenges.
Ready to Transform Your Manufacturing Operations? At Betamize, we specialize in helping businesses embrace Industry 4.0 technologies. Contact us today to explore how our innovative solutions can drive your manufacturing success and prepare you for the future.
Subscribe to my newsletter
Read articles from BetaMize directly inside your inbox. Subscribe to the newsletter, and don't miss out.
Written by
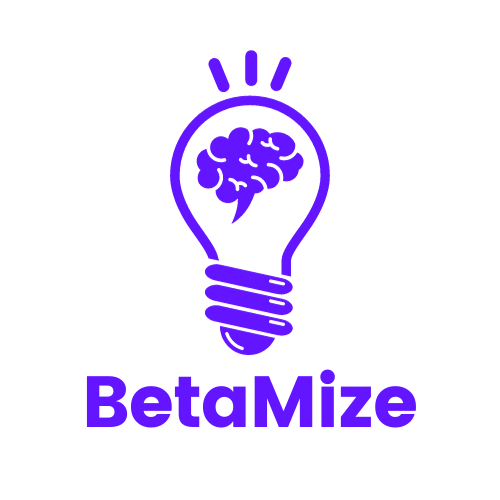