How Advanced Technologies Are Transforming the Future of Manufacturing
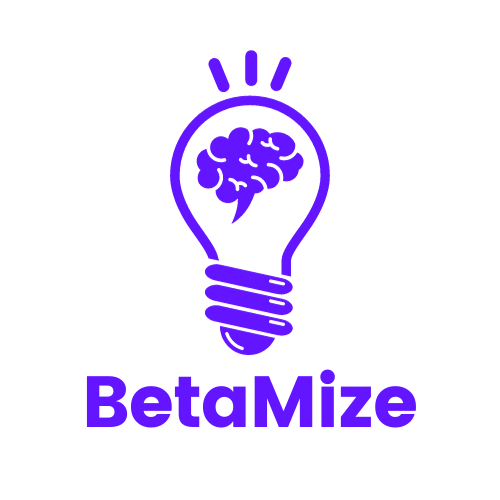
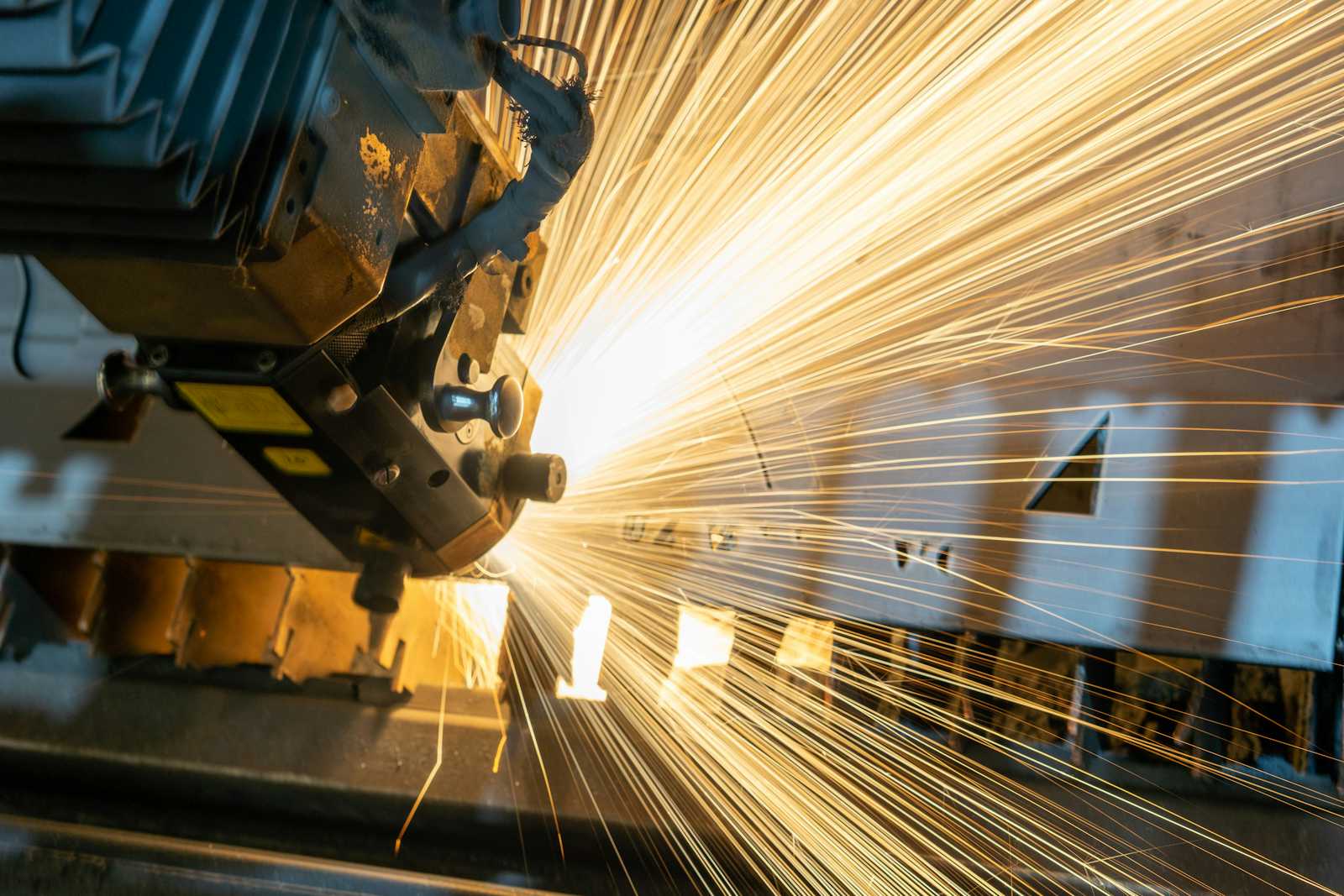
Industry 4.0, also known as the Fourth Industrial Revolution, is transforming the manufacturing landscape through the integration of advanced technologies. This revolution aims to create smarter, more efficient, and interconnected factories that can adapt to the ever-changing demands of the market. But what exactly are the technologies driving Industry 4.0? In this blog, we will explore the key technologies that are shaping the future of manufacturing and how they contribute to creating intelligent and responsive production environments.
1. Internet of Things (IoT)
The Foundation of Connectivity
The Internet of Things (IoT) is the backbone of Industry 4.0, enabling machines, devices, and systems to communicate and share data in real-time. IoT devices equipped with sensors and actuators collect valuable information about production processes, equipment health, and environmental conditions. This data is then transmitted to central systems where it can be analyzed and used to make informed decisions.
Benefits:
Real-time Monitoring: Continuous tracking of production parameters and equipment status.
Predictive Maintenance: Early detection of potential failures to reduce downtime.
Enhanced Efficiency: Optimizing resource usage and production processes.
2. Artificial Intelligence (AI) and Machine Learning
Driving Automation and Decision-Making
Artificial Intelligence (AI) and Machine Learning (ML) are at the core of Industry 4.0, enabling automated systems to learn from data, identify patterns, and make decisions without human intervention. AI algorithms can optimize production schedules, improve quality control, and predict maintenance needs.
Benefits:
Process Optimization: AI-driven analytics to enhance production efficiency.
Quality Control: Automated inspection and defect detection.
Predictive Analytics: Forecasting demand and maintenance requirements.
3. Big Data and Analytics
Harnessing the Power of Data
Big Data and Analytics play a crucial role in Industry 4.0 by processing vast amounts of data generated by IoT devices, machines, and other sources. Advanced analytics tools transform raw data into actionable insights, helping manufacturers understand trends, identify bottlenecks, and make data-driven decisions.
Benefits:
Informed Decision-Making: Leveraging data to optimize operations.
Improved Quality: Analyzing production data to enhance product quality.
Cost Reduction: Identifying inefficiencies and reducing waste.
4. Cyber-Physical Systems (CPS)
Integrating Physical and Digital Worlds
Cyber-Physical Systems (CPS) are integrated networks of physical devices and digital systems that interact in real-time. These systems enable seamless communication between machines, humans, and software, creating a unified and responsive manufacturing environment.
Benefits:
Real-Time Control: Synchronizing physical processes with digital commands.
Enhanced Flexibility: Quickly adapting to changes in production requirements.
Improved Safety: Monitoring and controlling processes to ensure safety.
5. Additive Manufacturing (3D Printing)
Revolutionizing Production Methods
Additive Manufacturing, commonly known as 3D Printing, is transforming traditional manufacturing processes by enabling the creation of complex and customized products with minimal waste. This technology allows manufacturers to produce prototypes, small batches, and even final products directly from digital designs.
Benefits:
Customization: Producing tailored products on-demand.
Reduced Waste: Minimizing material usage compared to traditional methods.
Speed to Market: Accelerating the prototyping and production process.
6. Cloud Computing
Enhancing Scalability and Collaboration
Cloud Computing provides the infrastructure and platforms necessary to store, process, and analyze data from anywhere in the world. This technology allows manufacturers to scale their operations, collaborate with partners, and access advanced computing resources without significant upfront investment.
Benefits:
Scalability: Easily adjusting resources based on demand.
Collaboration: Enabling seamless communication and data sharing.
Cost Efficiency: Reducing the need for expensive on-site hardware.
7. Augmented Reality (AR) and Virtual Reality (VR)
Transforming Training and Maintenance
Augmented Reality (AR) and Virtual Reality (VR) technologies are enhancing training, maintenance, and design processes in manufacturing. AR overlays digital information onto the physical world, while VR creates immersive virtual environments for simulations and training.
Benefits:
Improved Training: Providing realistic and interactive training experiences.
Enhanced Maintenance: Guiding technicians with real-time information.
Design and Prototyping: Visualizing and testing designs in virtual environments.
8. Robotics and Automation
Enhancing Precision and Efficiency
Advanced robotics and automation systems are central to Industry 4.0, performing repetitive, dangerous, and precise tasks with high accuracy and consistency. Collaborative robots (cobots) work alongside human operators, enhancing productivity and safety.
Benefits:
Increased Precision: Performing tasks with high accuracy.
Enhanced Productivity: Automating repetitive and time-consuming tasks.
Safety: Reducing human exposure to hazardous environments.
Conclusion
Industry 4.0 is revolutionizing manufacturing by integrating advanced technologies that enhance connectivity, automation, and data-driven decision-making. The combined power of IoT, AI, Big Data, CPS, additive manufacturing, cloud computing, AR/VR, and robotics is creating smarter, more efficient, and responsive production environments.
At Betamize, we are at the forefront of this revolution, offering innovative solutions to help manufacturers embrace the future of Industry 4.0. Contact us today to learn how our cutting-edge technologies can transform your manufacturing operations and drive your success.
Subscribe to my newsletter
Read articles from BetaMize directly inside your inbox. Subscribe to the newsletter, and don't miss out.
Written by
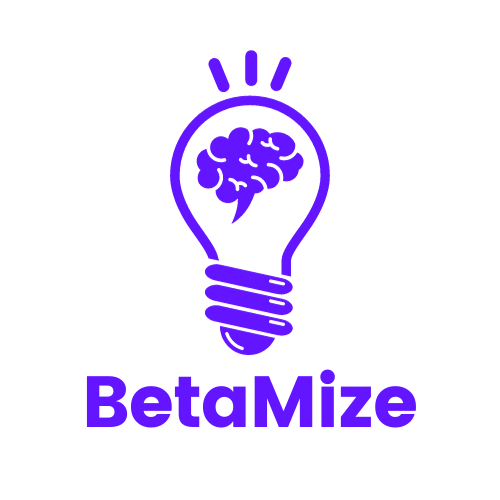