How Industrial Internet of Things (IIoT) is Revolutionizing Modern Manufacturing: Trends, Benefits, and Future Insights
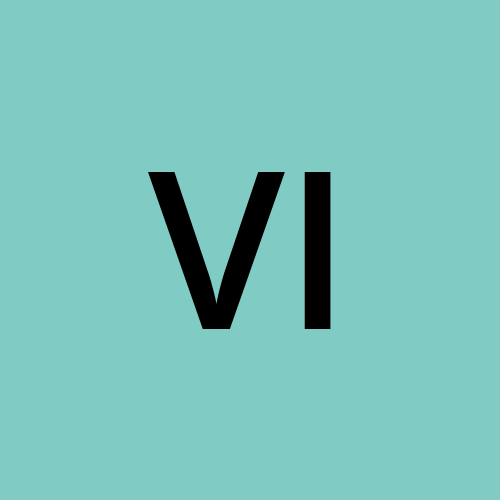
Table of contents
- Executive Summary
- I. Introduction
- II. The Evolution of IIoT
- III. IIoT Architecture and Components
- IV. The Role of IIoT in Manufacturing
- V. Data Analytics and AI in IIoT
- VI. The Impact of IIoT
- VII. IIoT Standards and Interoperability
- VIII. Vendors and System Survey
- IX. Challenges and Solutions
- X. IIoT Implementation Strategies
[IMAGE: Infographic showing the interconnected elements of IIoT in a manufacturing setting]
Executive Summary
The Industrial Internet of Things (IIoT) is revolutionizing the manufacturing sector by integrating internet-connected devices, sensors, and software to enhance operational efficiency and productivity. Key points include:
- Economic Impact: IIoT could add $14.2 trillion to the global economy by 2030 (Accenture report).
- Core Components: IIoT architecture comprises edge devices, edge computing, communication networks, cloud platforms, and analytics applications.
- Key Applications: Predictive maintenance, supply chain optimization, quality control automation.
- Data Analytics and AI: Enable powerful insights and decision-making capabilities, with some companies achieving up to 10% efficiency gains.
- Business Impact: Improved operational efficiency, enhanced productivity, increased profitability.
- Challenges: Data security, integration with legacy systems, high initial costs.
- Future Trends: Edge AI, 5G networks, digital twins.
Despite challenges, IIoT's potential benefits make it an indispensable component of the manufacturing industry's future, driving smarter and more responsive manufacturing processes.
I. Introduction
[IMAGE: Graph showing the projected growth of IIoT market size from 2020 to 2027]
The Industrial Internet of Things (IIoT) represents a transformative fusion of traditional manufacturing processes with advanced digital technology. IIoT involves the integration of internet-connected machinery, sensors, and software to collect and exchange data. This connectivity enables unprecedented levels of automation, data analysis, and operational efficiency.
In contemporary manufacturing, IIoT is crucial due to its potential to significantly enhance productivity, reduce operational costs, and improve product quality. The impact of IIoT on the manufacturing sector is substantial and growing:
- According to a report by Accenture, IIoT could add $14.2 trillion to the global economy by 2030, highlighting its immense economic potential.
- A study by PwC found that 91% of industrial companies are investing in digital factories, with 98% expecting to increase efficiency with integrated IIoT solutions.
- The global IIoT market size is projected to reach $263.4 billion by 2027, growing at a CAGR of 16.7% from 2020 to 2027 (Fortune Business Insights).
A prime example of IIoT's transformative power is Harley-Davidson's manufacturing plant in York, Pennsylvania. By implementing IIoT solutions, the company achieved:
- A reduction in the time to produce a motorcycle from 21 days to 6 hours
- An increase in production capacity from 7 to 25 motorcycles per shift
- A 7% increase in production effectiveness
- $200 million in cost savings
This case demonstrates how IIoT can dramatically improve manufacturing efficiency, flexibility, and profitability. As we delve deeper into the world of IIoT, we'll explore its evolution, key components, applications, and the challenges and opportunities it presents for the future of manufacturing.
II. The Evolution of IIoT
[IMAGE: Timeline showing the key milestones in the evolution of IIoT from the 1960s to present day]
The journey of IIoT began with the advent of industrial automation in the 1960s and 1970s, marked by the introduction of programmable logic controllers (PLCs) and distributed control systems (DCS). The 1990s saw the rise of industrial Ethernet, which improved communication and data exchange on the factory floor. The early 2000s introduced the concept of Machine-to-Machine (M2M) communication, laying the groundwork for today's IIoT.
Several key technological advancements have been pivotal in shaping the current state of IIoT:
Cloud Computing:
- Emerged in the mid-2000s, providing virtually unlimited storage and computing power.
- Enables IIoT systems to process and analyze vast amounts of data in real-time.
- Facilitates remote monitoring and control of manufacturing processes.
Big Data Analytics:
- Developed alongside the growth of digital data in the 2010s.
- Allows manufacturers to derive meaningful insights from the enormous volumes of data generated by IIoT devices.
- Enables predictive maintenance, quality control, and process optimization.
Advanced Sensor Technologies:
- Miniaturization and cost reduction of sensors in the 2010s made widespread deployment feasible.
- Enables real-time monitoring of various parameters (temperature, pressure, vibration, etc.) in manufacturing processes.
- Facilitates predictive maintenance and quality control.
5G Networks:
- The rollout of 5G networks beginning in 2019 has significantly enhanced connectivity capabilities.
- Provides higher bandwidth and lower latency, enabling more responsive and reliable IIoT systems.
- Facilitates the implementation of edge computing in industrial settings.
Artificial Intelligence and Machine Learning:
- The integration of AI and ML with IIoT data has accelerated since the mid-2010s.
- Enables advanced analytics, autonomous decision-making, and process optimization.
- Facilitates predictive maintenance, quality assurance, and supply chain optimization.
These technological advancements have collectively enabled real-time data processing, advanced predictive maintenance capabilities, and unprecedented levels of automation in manufacturing. As these technologies continue to evolve, they promise to further enhance the capabilities and impact of IIoT in the manufacturing sector.
III. IIoT Architecture and Components
[IMAGE: Diagram illustrating the layered architecture of IIoT systems]
IIoT architecture comprises several layers, each with distinct components that work together to facilitate seamless operation.
Edge Devices and Sensors: These devices collect data from manufacturing processes. Examples include temperature sensors, pressure gauges, and vibration sensors.
Edge Computing: This layer processes data locally, reducing latency and bandwidth usage. It involves microcontrollers and embedded systems.
Communication Networks: Reliable communication protocols such as MQTT, OPC-UA, and 5G ensure secure and fast data transmission.
Cloud Platforms: Data is aggregated and analyzed on cloud platforms, providing scalability and extensive storage capabilities.
Analytics and Applications: Big data analytics and AI applications derive insights from data, driving decision-making processes.
In a real-world scenario, sensors on a production line might detect anomalies in machinery vibration, triggering predictive maintenance protocols to prevent equipment failure.
IV. The Role of IIoT in Manufacturing
[IMAGE: Infographic showing the key applications of IIoT in manufacturing]
IIoT has revolutionized various aspects of manufacturing through its diverse applications. Here are some key areas with real-world examples:
Predictive Maintenance:
- By continuously monitoring equipment health, IIoT can predict failures before they occur, reducing downtime.
- Case Study: Rolls-Royce implemented IIoT-enabled predictive maintenance for their aircraft engines. By analyzing data from sensors, they can predict when an engine needs servicing, reducing unscheduled maintenance by 25% and improving overall efficiency.
Supply Chain Optimization:
- Real-time tracking of materials and products enhances supply chain visibility and efficiency.
- Example: Caterpillar uses IIoT to track the location and condition of its heavy machinery across global supply chains. This has improved inventory management and reduced logistics costs by 10%.
Quality Control:
- Automated inspection systems use IIoT data to detect defects early in the production process, ensuring higher quality standards.
- Case Study: BMW implemented an IIoT-based quality control system in its paintshop. By using connected sensors and real-time data analysis, they reduced paint defects by 30% and improved overall product quality.
V. Data Analytics and AI in IIoT
[IMAGE: Flowchart showing how data flows from IIoT devices through analytics to actionable insights]
The integration of big data analytics and AI within IIoT systems allows for powerful insights and decision-making capabilities.
Predictive Analytics:
- Analyzing historical data to forecast future events, such as equipment failures or demand fluctuations.
- Example: John Deere uses predictive analytics in its agricultural equipment. By analyzing data from soil sensors and weather patterns, they help farmers optimize planting and harvesting times, increasing crop yields by up to 15%.
Machine Learning:
- Algorithms learn from data patterns to optimize manufacturing processes and improve product quality.
- Case Study: Siemens uses AI-driven analytics to enhance the performance of its gas turbines. By analyzing operational data and optimizing parameters in real-time, they achieved up to 10% efficiency gains and reduced emissions.
VI. The Impact of IIoT
[IMAGE: Bar chart comparing key performance indicators before and after IIoT implementation]
IIoT has profound impacts on manufacturing efficiency, productivity, and profitability:
Efficiency:
- Real-time monitoring and automation reduce waste and energy consumption.
- Case Study: Harley-Davidson improved its operational efficiency by 80% after implementing IIoT solutions in its York, Pennsylvania plant. They reduced the time to produce a motorcycle from 21 days to just 6 hours.
Productivity:
- Automation of routine tasks frees up human resources for more complex roles, boosting overall productivity.
- Example: Intel implemented IIoT in its semiconductor manufacturing facilities, resulting in a 2% increase in yield and $30 million in cost savings annually.
Profitability:
- Enhanced efficiency and productivity directly contribute to higher profit margins.
- Case Study: General Electric's implementation of IIoT in its battery manufacturing plant led to a 4% increase in production output and $2 million in annual savings.
VII. IIoT Standards and Interoperability
[IMAGE: Diagram showing how different IIoT standards interact in a manufacturing ecosystem]
Standards and interoperability are critical for the seamless functioning of IIoT systems. Key standards include:
- OPC-UA (Open Platform Communications Unified Architecture): Ensures secure and reliable data exchange.
- MQTT (Message Queuing Telemetry Transport): Lightweight protocol ideal for connecting remote devices.
Interoperability allows different systems and devices to communicate and work together, essential for scalable and flexible IIoT deployments.
VIII. Vendors and System Survey
[IMAGE: Comparison chart of major IIoT platform providers]
A comparison of major IIoT platform providers:
Vendor | Pros | Cons |
Vendor A | Comprehensive solutions, strong analytics | High cost |
Vendor B | Robust cloud infrastructure, scalability | Complexity in implementation |
Vendor C | Advanced AI capabilities, extensive support | Expensive for small to mid-sized companies |
Vendor D | User-friendly, quick deployment | Limited customization options |
Selecting the right vendor involves evaluating factors such as scalability, ease of integration, and cost.
IX. Challenges and Solutions
[IMAGE: Infographic illustrating common IIoT challenges and their solutions]
While IIoT offers numerous benefits, its implementation comes with significant challenges. Among these, cybersecurity stands out as a critical concern:
1. Cybersecurity in IIoT
The interconnected nature of IIoT systems expands the attack surface for potential cyber threats. Key challenges include:
a) Diverse Attack Vectors:
- Threat: IIoT networks often include a wide range of devices, each potentially serving as an entry point for attackers.
- Example: In 2017, a malware attack on a petrochemical facility exploited vulnerabilities in industrial control systems.
b) Data Privacy and Protection:
- Threat: Unauthorized access to sensitive manufacturing data can lead to intellectual property theft or competitive disadvantages.
- Case Study: In 2018, an automotive manufacturer fell victim to a crypto-mining malware attack through a poorly secured cloud console, exposing sensitive data.
c) Legacy System Integration:
- Challenge: Older systems may lack modern security features, creating vulnerabilities when integrated into IIoT networks.
d) Supply Chain Vulnerabilities:
- Threat: Attacks on suppliers or third-party components can compromise the entire manufacturing process.
- Example: A major supply chain attack in 2020 affected numerous organizations, including manufacturing firms.
Prevention Strategies and Best Practices:
Implement a Zero Trust Architecture:
- Approach: Treat all network traffic as potentially malicious, requiring verification for every access attempt.
- Example: Implement strong authentication methods like multi-factor authentication (MFA) for all IIoT system access.
Segmentation and Isolation:
- Strategy: Divide the network into separate segments to contain potential breaches.
- Implementation: Use virtual LANs (VLANs) or software-defined networking (SDN) to isolate critical systems.
Regular Security Audits and Penetration Testing:
- Practice: Conduct frequent assessments to identify and address vulnerabilities.
- Example: Perform regular red team exercises to test the security of IIoT systems.
Encryption and Secure Protocols:
- Approach: Ensure all data transmission within the IIoT network is encrypted.
- Implementation: Use protocols like TLS/SSL for data in transit and implement robust encryption for data at rest.
Continuous Monitoring and Incident Response:
- Strategy: Implement real-time monitoring systems to detect and respond to security incidents quickly.
- Tool: Security Information and Event Management (SIEM) systems can help in real-time threat detection.
Regular Software Updates and Patch Management:
- Practice: Keep all IIoT devices and systems updated with the latest security patches.
- Challenge: Coordinate updates to minimize production disruptions while maintaining security.
Employee Training and Awareness:
- Approach: Educate staff about cybersecurity risks and best practices.
- Example: Implement regular phishing simulations and security awareness training programs.
Secure by Design Principle:
- Strategy: Incorporate security considerations from the initial stages of IIoT system design.
- Implementation: Use secure development practices and conduct security reviews throughout the development lifecycle.
By implementing these strategies and best practices, manufacturers can significantly enhance the security of their IIoT systems, protecting against potential cyber threats while reaping the benefits of increased connectivity and data-driven insights.
X. IIoT Implementation Strategies
[IMAGE: Flowchart illustrating the steps of IIoT implementation]
Implementing IIoT in a manufacturing environment requires a strategic approach. Here's a step-by-step guide to help companies navigate the implementation process:
1. Assessment and Planning
a) Current State Analysis:
- Evaluate existing infrastructure, processes, and technology stack.
- Identify pain points and areas for improvement.
b) Goal Setting:
- Define clear, measurable objectives for IIoT implementation (e.g., reduce downtime by 20%, improve overall equipment effectiveness by 15%).
- Align IIoT goals with broader business objectives.
c) Stakeholder Engagement:
- Involve key stakeholders from IT, operations, management, and shop floor.
- Address concerns and gather input to ensure buy-in across the organization.
d) ROI Analysis:
- Conduct a cost-benefit analysis to justify the investment.
- Consider both short-term gains and long-term strategic advantages.
2. Design and Architecture
a) IIoT Architecture Design:
- Develop a comprehensive IIoT architecture that addresses connectivity, data collection, storage, and analytics.
- Ensure scalability and flexibility to accommodate future growth.
b) Security Planning:
- Incorporate security measures from the outset (refer to cybersecurity best practices in previous section).
- Design with a "security-first" mindset.
c) Integration Strategy:
- Plan for seamless integration with existing systems (ERP, MES, SCADA, etc.).
- Develop APIs and middleware solutions as needed.
3. Pilot Implementation
a) Start Small:
- Begin with a pilot project in a specific area or production line.
- Choose an application with high potential impact and relatively low risk.
b) Sensor and Device Selection:
- Identify and procure appropriate sensors and IIoT devices for the pilot.
- Ensure compatibility with existing equipment and planned architecture.
Subscribe to my newsletter
Read articles from Vikas directly inside your inbox. Subscribe to the newsletter, and don't miss out.
Written by
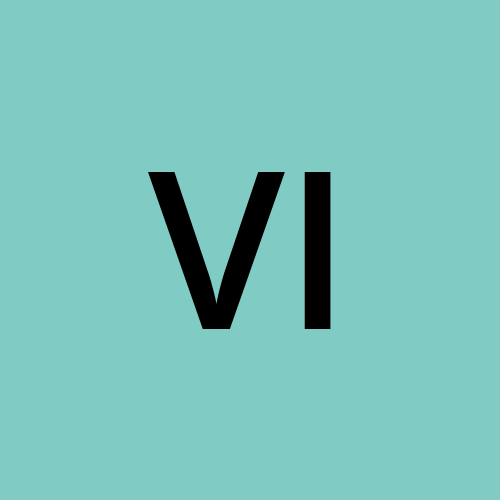