Leveraging AI Analytics for Predictive Maintenance in Manufacturing

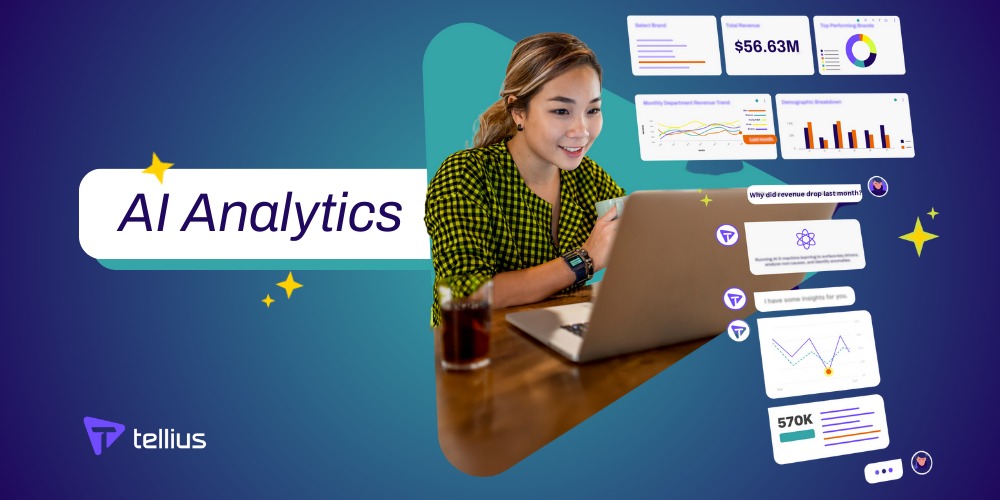
Predictive maintenance has become a game-changer in the manufacturing industry, offering a proactive approach to equipment management that reduces downtime, minimizes costs, and enhances overall efficiency. At the heart of this innovation is AI analytics, which enables manufacturers to predict equipment failures before they happen, ensuring that machinery operates at peak performance.
The Traditional Approach: Reactive vs. Preventive Maintenance
For decades, manufacturers have relied on reactive and preventive maintenance strategies to keep their equipment running. Reactive maintenance involves repairing or replacing machinery only after it breaks down, leading to unplanned downtime, costly repairs, and potential disruptions to the production schedule. On the other hand, preventive maintenance involves performing regular, scheduled maintenance based on time intervals or usage levels, regardless of the actual condition of the equipment. While preventive maintenance is more proactive, it can still result in unnecessary maintenance activities and does not account for the actual wear and tear on machinery.
The Rise of Predictive Maintenance
Predictive maintenance takes equipment management to the next level by using AI-driven analytics to monitor the condition of machinery in real-time. By analyzing data from sensors embedded in the equipment, AI algorithms can detect patterns and anomalies that indicate potential failures. This allows manufacturers to perform maintenance only when it is needed, based on the actual condition of the machinery, rather than on a fixed schedule.
How AI Analytics Enhances Predictive Maintenance
AI analytics plays a critical role in predictive maintenance by processing vast amounts of data generated by industrial equipment. These data points include temperature, vibration, pressure, and other key performance indicators that provide insights into the health of the machinery. Here’s how AI analytics enhances predictive maintenance:
Real-Time Monitoring: AI-powered sensors continuously monitor equipment performance, collecting data on various parameters that affect the machinery's operation. This real-time monitoring allows manufacturers to detect issues as they arise, preventing minor problems from escalating into major failures.
Pattern Recognition: AI algorithms are adept at recognizing patterns in data that may be too subtle for humans to detect. By analyzing historical data and identifying trends, AI can predict when a piece of equipment is likely to fail, giving manufacturers ample time to schedule maintenance and order replacement parts.
Anomaly Detection: One of the most powerful features of AI analytics is its ability to detect anomalies in equipment performance. These anomalies can be early indicators of potential failures, such as unusual vibrations or temperature fluctuations. By identifying these warning signs early, manufacturers can take corrective action before a breakdown occurs.
Optimized Maintenance Schedules: Predictive maintenance driven by AI analytics allows manufacturers to optimize their maintenance schedules. Instead of adhering to a rigid, time-based maintenance plan, manufacturers can schedule maintenance activities based on the actual condition of the equipment. This reduces unnecessary maintenance and ensures that resources are used more efficiently.
The Benefits of AI-Driven Predictive Maintenance
The adoption of AI-driven predictive maintenance offers numerous benefits to manufacturers:
Reduced Downtime: By predicting and preventing equipment failures, AI analytics helps minimize unplanned downtime, keeping production lines running smoothly.
Cost Savings: Predictive maintenance reduces the need for emergency repairs and extends the lifespan of equipment, resulting in significant cost savings.
Improved Safety: By identifying potential failures before they occur, predictive maintenance enhances workplace safety by reducing the risk of accidents caused by faulty machinery.
Increased Efficiency: Optimized maintenance schedules ensure that machinery operates at peak efficiency, leading to higher productivity and better overall performance.
AI analytics is revolutionizing predictive maintenance in manufacturing, providing a powerful tool for optimizing equipment management. By leveraging real-time data, pattern recognition, and anomaly detection, AI-driven predictive maintenance helps manufacturers reduce downtime, lower costs, and improve safety. As the manufacturing industry continues to embrace digital transformation, AI analytics will play an increasingly important role in driving efficiency and competitiveness.
Subscribe to my newsletter
Read articles from Tellius Usa directly inside your inbox. Subscribe to the newsletter, and don't miss out.
Written by
