Manufacturing Execution Systems (MES)
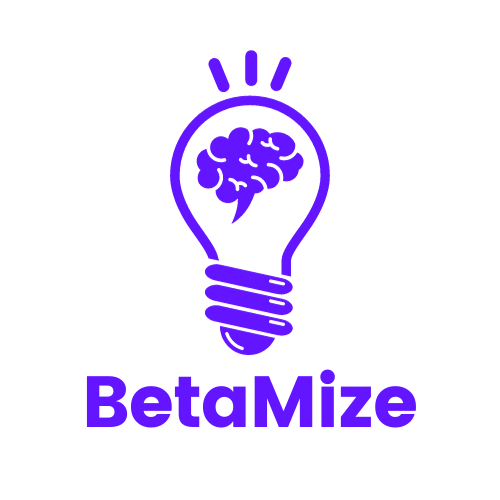
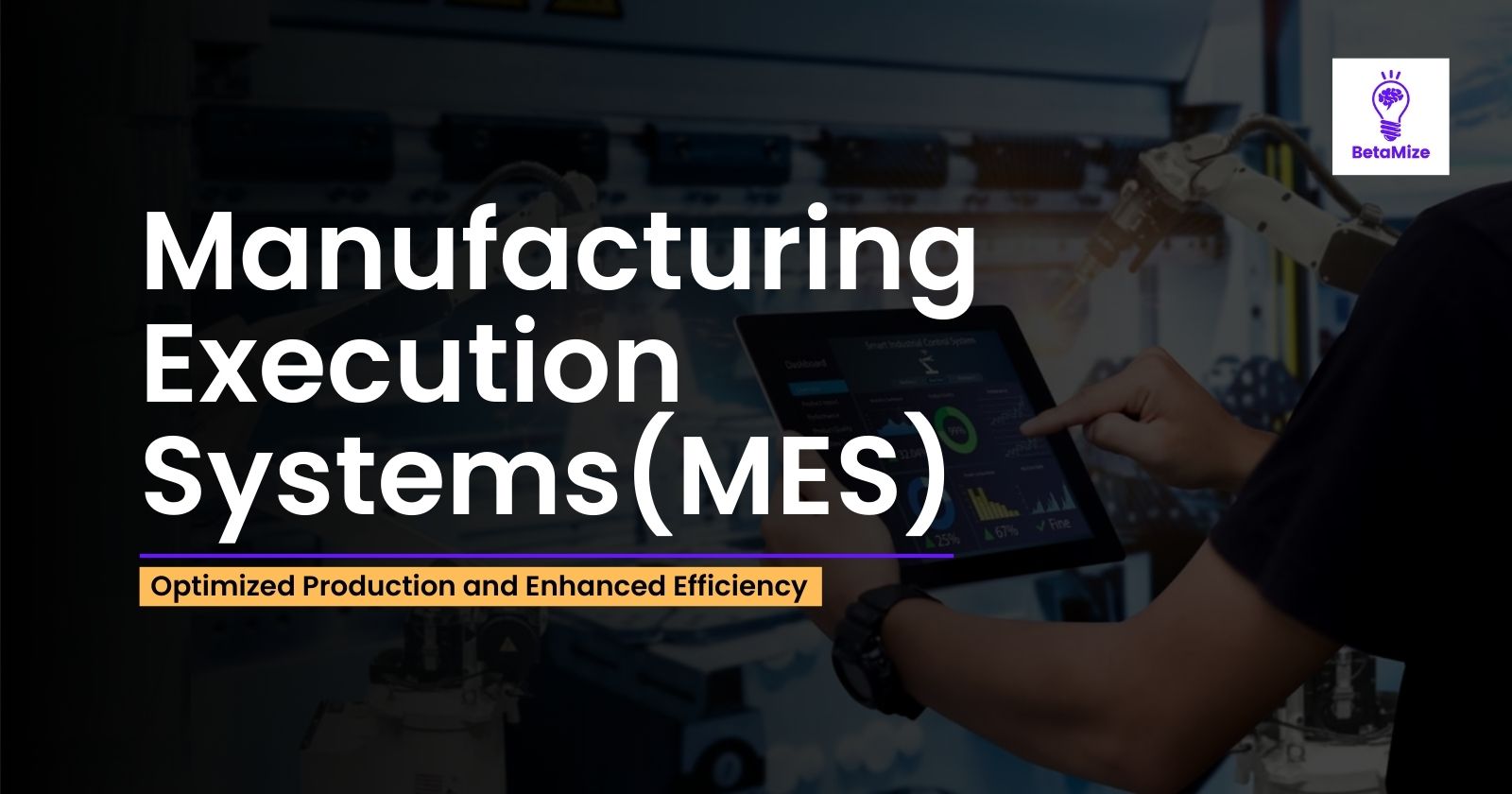
Manufacturing Execution Systems (MES): The Key to Optimized Production and Enhanced Efficiency
In today’s rapidly evolving manufacturing landscape, staying competitive requires more than just operational efficiency—it demands the integration of advanced technology and systems to manage, monitor, and control manufacturing processes in real-time. This is where Manufacturing Execution Systems (MES) play a pivotal role.
MES is a powerful tool that bridges the gap between enterprise resource planning (ERP) systems and shop floor control systems. It provides manufacturers with detailed insights into production processes, allowing for better decision-making, improved efficiency, and higher product quality.
This article will explore what MES is, how it works, its benefits, and why it’s crucial for modern manufacturing operations.
What is a Manufacturing Execution System (MES)?
A Manufacturing Execution System (MES) is a software solution designed to monitor, track, and control production in real-time. It connects machines, people, and systems on the shop floor to ensure that manufacturing operations are as efficient as possible. MES solutions cover various aspects of the manufacturing process, including scheduling, inventory management, production execution, and quality control.
MES serves as the intermediary between the shop floor and higher-level systems like Enterprise Resource Planning (ERP), providing real-time data to help companies optimize their production processes. It captures and analyzes production data, offering insights into performance, bottlenecks, and areas for improvement.
Key Features of MES
Real-Time Production Monitoring
- MES allows manufacturers to track the progress of production in real-time. It monitors the performance of machines, workforce, and materials to ensure smooth and efficient operations.
Production Scheduling and Dispatching
- MES ensures that production schedules are adhered to by providing detailed scheduling capabilities. It automatically dispatches tasks to the shop floor, helping optimize resource allocation and machine utilization.
Inventory and Materials Management
- MES keeps track of raw materials and finished goods inventory in real-time, ensuring accurate stock levels. This feature helps avoid production delays due to material shortages and reduces the risk of overproduction.
Quality Control
- MES systems include quality management tools to ensure products meet specific standards. By monitoring product quality at every stage of production, MES helps reduce defects and waste.
Data Collection and Reporting
- MES collects real-time data on production activities, machine performance, and workforce efficiency. This data is then used to generate reports that provide actionable insights into the manufacturing process.
Compliance and Traceability
- MES ensures that manufacturers can meet industry regulations by offering traceability for each product and batch. It allows for quick and accurate recall in the event of quality issues.
Performance Analysis
- MES enables manufacturers to analyze key performance indicators (KPIs) such as overall equipment effectiveness (OEE), cycle times, and downtime, leading to more informed decision-making.
How MES Works
MES integrates with various systems and machinery on the shop floor to provide a complete overview of production activities. It collects data from equipment, production lines, and employees to deliver real-time insights into production status, machine health, and operator performance.
Here’s how MES typically functions:
Data Collection: MES gathers data from machines, sensors, and human inputs at each stage of the production process.
Data Analysis: The system analyzes this data to identify inefficiencies, monitor progress, and detect any deviations from the production plan.
Task Dispatching: MES uses the data to dispatch tasks, ensuring that the right materials, tools, and instructions are sent to the appropriate operators and machines.
Real-Time Monitoring: MES provides real-time visibility into the status of machines, work orders, and products. Any disruptions or inefficiencies can be addressed immediately.
Reporting: MES generates reports and dashboards to help management understand production performance, resource utilization, and quality levels.
Benefits of MES for Manufacturers
Improved Production Efficiency
- MES automates manual processes and reduces downtime, leading to higher productivity. By optimizing resource use, MES ensures that production runs smoothly without delays or interruptions.
Real-Time Visibility
- MES provides manufacturers with a real-time view of their shop floor operations. This visibility allows for quick responses to issues like machine malfunctions, material shortages, or quality control failures.
Higher Product Quality
- With built-in quality control measures, MES ensures that products meet required specifications. By catching defects early in the process, manufacturers can reduce waste and improve overall product quality.
Enhanced Compliance and Traceability
- MES ensures that manufacturers can trace each product from raw material to finished goods. This traceability is essential for industries with strict regulatory requirements, such as food, pharmaceuticals, and automotive.
Cost Reduction
- By improving efficiency, reducing waste, and minimizing downtime, MES helps manufacturers lower their operating costs. It also optimizes inventory management, reducing the costs associated with excess stock or material shortages.
Better Decision-Making
- With access to real-time data and reports, decision-makers can identify bottlenecks, predict future trends, and make informed choices about production processes. MES enhances strategic planning and resource allocation.
Seamless Integration with ERP Systems
- MES integrates easily with ERP systems, ensuring a smooth flow of information between the shop floor and management. This integration allows manufacturers to synchronize production with overall business goals.
Why MES is Essential in Modern Manufacturing
The manufacturing industry is undergoing significant transformation, driven by digital technologies, automation, and Industry 4.0. As production processes become more complex, manufacturers need tools that can provide real-time insights and automation to remain competitive.
MES plays a crucial role in modern manufacturing for several reasons:
Adaptation to Industry 4.0: As manufacturing moves towards Industry 4.0, the integration of cyber-physical systems, IoT, and automation becomes critical. MES enables this by offering real-time data collection, advanced analytics, and automated workflows.
Managing Global Supply Chains: MES allows manufacturers to manage operations across multiple locations, making it easier to track production activities, coordinate resources, and ensure consistency in quality.
Customization and Flexibility: With customer demands becoming more personalized, manufacturers must have flexible production systems. MES allows for customized workflows and agile production planning to meet changing customer requirements.
Sustainability Goals: MES helps companies optimize resource use, reduce waste, and ensure energy-efficient production processes, contributing to sustainability initiatives.
Conclusion: Embrace MES for Operational Excellence
Manufacturing Execution Systems (MES) are critical for any manufacturer looking to optimize production processes, reduce waste, and improve product quality. By providing real-time insights, automating workflows, and ensuring compliance, MES offers a competitive advantage in an increasingly complex industry.
Ready to take your manufacturing operations to the next level? Explore the innovative MES solutions at Betamize and see how our technology can transform your shop floor for greater efficiency and productivity. Contact us today to learn more about how MES can benefit your business.
Subscribe to my newsletter
Read articles from BetaMize directly inside your inbox. Subscribe to the newsletter, and don't miss out.
Written by
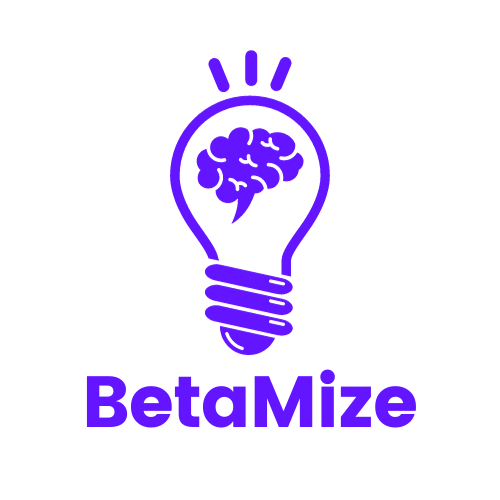