AI-Powered Defect Detection: Advancements in Machine Learning Algorithms
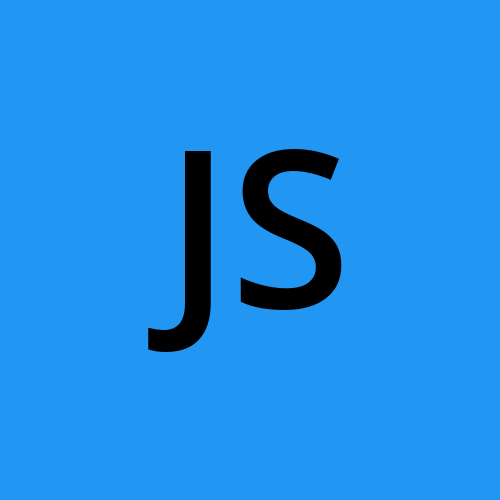
In today's fast-paced world of manufacturing, quality control is a cornerstone for ensuring product reliability, customer satisfaction, and cost-efficiency. Traditional methods of defect detection, primarily reliant on manual inspection and vision inspection systems in manufacturing, often struggle with complexity, subtlety in defect patterns, and scalability. These systems, while effective for certain tasks, can be prone to errors and inefficiencies. However, the advent of AI-powered defect detection is transforming how industries monitor and ensure product quality, making the process faster, more accurate, and adaptable.
This blog explores how AI-driven defect detection works, recent advancements in machine learning algorithms powering these systems, and the transformative impact on manufacturing and beyond.
The Importance of Defect Detection
Defects in products can lead to substantial financial losses, recalls, and damage to brand reputation. Traditional quality control methods, including manual inspection and early-generation vision systems, are prone to human error, inconsistency, and can be time-consuming. These limitations become even more pronounced in industries where high-volume production and precision are required.
AI-powered defect detection addresses these challenges by leveraging machine learning algorithms to automate inspection processes, reduce human errors, and enhance scalability. This allows manufacturers to identify defects quickly and consistently.
How AI-Powered Defect Detection Works
AI-powered defect detection systems use machine learning models to analyze images, videos, or sensor data from production lines. Here’s a general process breakdown:
1. Data Collection: High-resolution images or sensor data are collected from production lines using cameras or sensors to monitor product quality.
2. Model Training: Machine learning algorithms, often based on deep learning techniques like Convolutional Neural Networks (CNNs), are trained on labeled data (e.g., images of defective and non-defective products). The model learns to detect specific patterns and deviations that signify defects.
3. Real-Time Detection: After training, the model is deployed to run in real-time, scanning products as they are manufactured. It can quickly identify defects with high accuracy, ensuring faulty products are removed from the production line.
4. Continuous Learning: The system improves over time by incorporating new defect data, becoming more robust and adaptive to evolving defect types or manufacturing changes.
Advancements in Machine Learning Algorithms
Recent advancements in machine learning have made AI-powered defect detection more efficient and accurate. Here are some key innovations driving this technology forward:
- Deep Learning and Convolutional Neural Networks (CNNs)
Deep learning has revolutionized image-based defect detection, particularly through the use of CNNs. Unlike traditional vision systems that rely on predefined rules, CNNs automatically learn to detect features from raw images, which improves their ability to identify subtle and complex defects. CNNs can handle various challenges, such as inconsistencies in lighting, textured surfaces, or minute defects that are difficult to detect with traditional methods.
- Transfer Learning
Transfer learning has proven to be especially valuable for defect detection in industries where collecting large amounts of labeled data is challenging. Instead of training models from scratch, pre-trained models (often based on large datasets like ImageNet) can be fine-tuned for specific defect detection tasks. This reduces training time and improves the accuracy of AI systems in identifying defects.
- Unsupervised and Semi-Supervised Learning
In many cases, labeled defect data can be scarce, which makes supervised learning less effective. Unsupervised learning algorithms allow AI models to learn from unlabeled data, identifying anomalies or deviations from normal patterns. Semi-supervised learning, which combines labeled and unlabeled data, further enhances defect detection performance when only a small set of labeled data is available.
- Anomaly Detection
Anomaly detection is crucial in industries where defects are rare but costly, such as electronics or aerospace. By training models to recognize normal behavior, deviations or anomalies are flagged as potential defects. This approach is particularly useful for detecting new or unusual defects that have not been previously seen in the training data.
- Edge Computing for Real-Time Detection
For industries that require real-time monitoring, edge computing enables defect detection algorithms to run directly on devices, such as cameras or sensors, located at the production line. This eliminates the latency associated with cloud processing, ensuring that defective products are identified instantly, even in high-speed production environments.
- Explainability and Interpretability
As AI models become more complex, ensuring they are interpretable is essential, especially in regulated industries like healthcare or aerospace. Innovations such as saliency maps and Grad-CAM (Gradient-weighted Class Activation Mapping) help visualize the parts of the image the model considers defective. This increases transparency and trust in AI-powered defect detection systems.
Impact on Manufacturing Industries
AI-powered defect detection is making significant waves across various industries by enhancing accuracy, reducing costs, and improving operational efficiency:
- Automotive: Identifying tiny cracks, weld defects, or misaligned parts during assembly.
- Electronics: Detecting soldering issues, component misalignment, and surface defects in PCB production.
- Textiles: Spotting irregularities in fabric patterns, dye inconsistencies, or tears.
- Food and Beverage: Ensuring proper packaging, labeling, and checking for contamination.
- Healthcare: Detecting micro-defects in medical devices or analyzing diagnostic images in real time.
By integrating AI-driven systems, industries benefit from faster quality control processes, less human error, and improved product consistency.
The Future of AI-Powered Defect Detection
Looking forward, AI-powered defect detection will continue to evolve alongside advancements in machine learning algorithms. Technologies like federated learning, where models learn collaboratively across multiple devices without sharing sensitive data, and quantum computing, which could solve complex optimization problems faster, are on the horizon.
Furthermore, as vision inspection systems in manufacturing become more integrated into broader Industry 4.0 frameworks, manufacturers will experience increased automation, predictive analytics, and enhanced decision-making. Future defect detection systems could potentially offer self-healing production lines, where defects are anticipated and corrected before they even occur.
Conclusion
AI-powered defect detection, supported by advancements in machine learning algorithms, is transforming quality control across manufacturing industries. With deep learning, real-time processing, and anomaly detection capabilities, AI is making defect detection faster, more accurate, and scalable. These innovations are helping industries enhance their vision inspection systems in manufacturing, enabling them to reduce costs, improve product quality, and drive efficiency.
As these technologies continue to mature, AI-powered defect detection will become a cornerstone of modern manufacturing, offering smarter, more reliable, and autonomous systems that can detect and correct defects in real time.
Subscribe to my newsletter
Read articles from John Smith directly inside your inbox. Subscribe to the newsletter, and don't miss out.
Written by
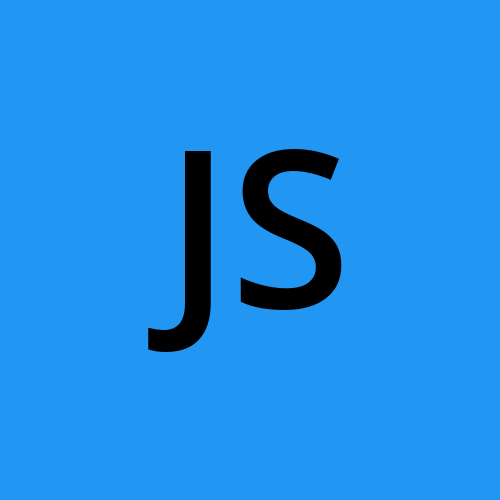