Quality assurance vs. quality control: Key differences and delivering excellence
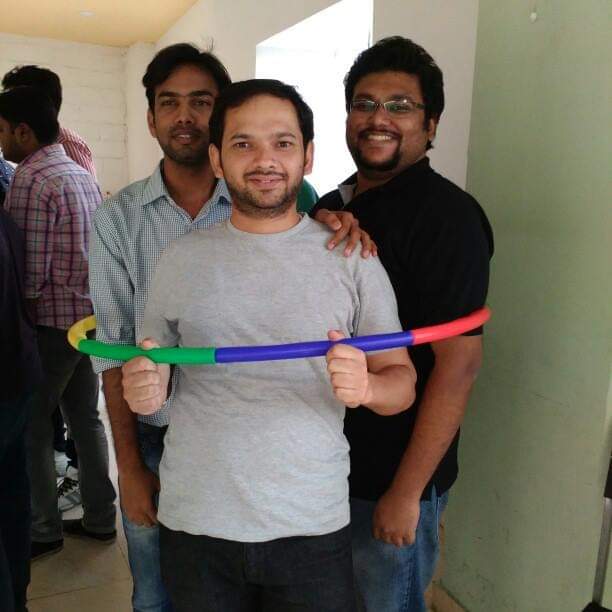
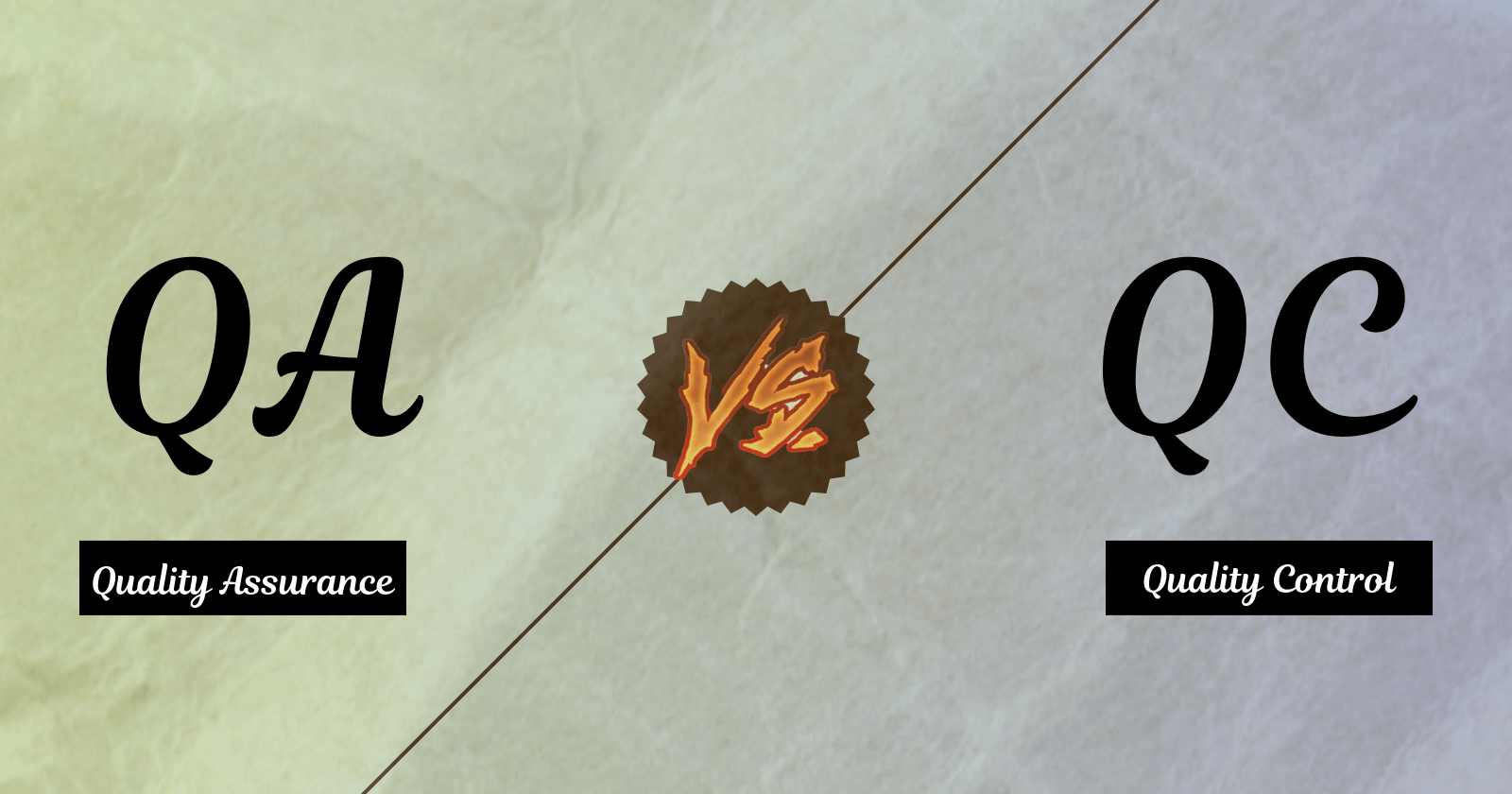
In the world of manufacturing, software development, and various service industries, two terms often surface with significant weight: Quality Assurance (QA) and Quality Control (QC). While both play crucial roles in ensuring the delivery of high-quality products and services, they are not interchangeable. Understanding the key differences between QA and QC is essential for any organization striving for excellence. This blog post delves into the nuances of both concepts, highlighting their importance and how they complement each other in the pursuit of quality.
What is Quality Assurance (QA)?
Quality Assurance refers to the set of processes and procedures aimed at ensuring the quality of products or services from the beginning stages of production or development. It is a proactive, process-oriented approach that focuses on preventing defects before they occur. QA involves the systematic planning, implementation, and monitoring of processes, with a keen eye on meeting the defined standards and specifications. This approach emphasizes the improvement of the production process itself and requires a company-wide commitment to quality.
Key aspects of QA include:
Process Evaluation and Improvement: Regular analysis and improvement of workflows, procedures, and standards to enhance quality.
Training and Development: Ensuring that all team members are equipped with the necessary knowledge and skills to maintain quality standards.
Documentation: Keeping detailed records of processes, changes, and improvements to ensure consistency and accountability.
What is Quality Control (QC)?
Quality Control, on the other hand, is the process of identifying defects in the final products or services before they reach the customer. It is a reactive, product-oriented approach that involves inspection, testing, and correction of products or services to ensure they meet the quality standards set by the organization. QC is typically conducted by a dedicated team of inspectors or testers who evaluate the outputs to identify any deviations from the quality specifications.
Key aspects of QC include:
Inspection and Testing: Examining finished products or services for defects or non-compliance with quality standards.
Defect Identification: Pinpointing and documenting specific issues or deviations in products or services.
Corrective Actions: Implementing fixes or making decisions to discard defective products to ensure that only quality items reach the customer.
The Interplay Between QA and QC
While QA and QC serve different functions, they are complementary and both are vital to an organization’s quality management system. QA lays the groundwork for quality by establishing robust processes and procedures that minimize the chance of defects. QC, meanwhile, acts as the final checkpoint to catch any discrepancies and ensure that the end product meets the desired standards of quality.
Strategic Alignment and Objectives
Unified Goals: Both QA and QC align with the overarching goal of delivering products and services that meet or exceed customer expectations. While QA focuses on the processes to prevent defects, QC concentrates on identifying defects in the final output. Together, they ensure that quality objectives are met consistently.
Continuous Feedback Loop
Feedback for Continuous Improvement: QC provides critical feedback to the QA processes. When QC identifies defects or areas for improvement in the products or services, this information is fed back to improve the QA processes and prevent similar issues in the future. This creates a continuous loop of improvement, where the lessons learned from QC directly influence and enhance QA practices.
Risk Management
Proactive and Reactive Risk Mitigation: QA’s proactive approach helps in identifying potential risks and implementing preventive measures early in the production cycle. QC, with its reactive stance, manages risks by catching and addressing defects before products reach the customers. This dual approach to risk management ensures comprehensive coverage and minimizes the likelihood of quality failures.
Cross-functional Collaboration
Enhanced Communication and Collaboration: The successful interplay between QA and QC requires effective communication and collaboration across different departments within an organization. By fostering a culture of quality that transcends departmental boundaries, organizations can ensure that everyone is aligned toward common quality objectives, leading to more cohesive and effective quality management.
Data-Driven Decision Making
Leveraging Data for Improvement: Both QA and QC generate valuable data about the production process and the final product quality. By analyzing this data, organizations can identify trends, pinpoint areas for improvement, and make informed decisions to refine their processes and products. This data-driven approach supports strategic decision-making and the continuous enhancement of quality standards.
The interplay between QA and QC is not just a matter of fulfilling procedural requirements; it represents a holistic approach to quality management that leverages the strengths of both to achieve excellence. By understanding and optimizing this interplay, organizations can ensure the consistent delivery of high-quality products and services, fostering trust and satisfaction among their customers.
The Importance of QA and QC in Delivering Excellence
Implementing both QA and QC is crucial for any organization aiming for excellence. Here’s why:
Customer Satisfaction: Ensuring the delivery of high-quality products or services enhances customer satisfaction and loyalty.
Efficiency and Cost Savings: By preventing defects early on, organizations can save on the costs associated with rework, returns, and repairs.
Reputation and Competitiveness: A commitment to quality can significantly enhance a company’s reputation and give it a competitive edge in the market.
Regulatory Compliance: Many industries are subject to stringent regulatory standards that govern the quality of products and services. QA and QC are critical in ensuring compliance with these regulations, helping organizations avoid legal penalties, fines, and damage to their reputation.
Risk Management: By identifying potential issues early in the process (QA) and before the product reaches the customer (QC), companies can significantly mitigate risks associated with product failures, safety issues, and recalls. This proactive and reactive approach to quality can save an organization from costly damages and protect its brand integrity.
Integrating QA and QC into the core of an organization’s operations underlines a commitment to excellence that goes beyond mere compliance or standardization. It signifies a dedication to exceeding expectations, improving continuously, and delivering products and services that stand out in the crowded marketplace.
Conclusion
Quality Assurance and Quality Control are two sides of the same coin, each playing a distinct yet interrelated role in the quest for quality. By understanding and implementing both concepts effectively, organizations can not only meet but exceed the expectations of their customers, ensuring the delivery of exceptional products and services. In a world where quality is a key differentiator, mastering the dynamics of QA and QC is a prerequisite for success.
Source: This information was first published here https://www.londondaily.news/quality-assurance-vs-quality-control-key-differences-and-delivering-excellence/
Subscribe to my newsletter
Read articles from Abhay directly inside your inbox. Subscribe to the newsletter, and don't miss out.
Written by
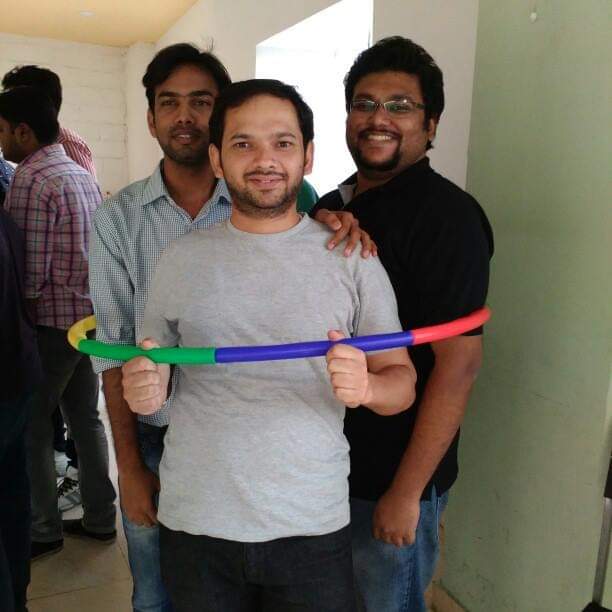
Abhay
Abhay
I am a digital marketer with 13+ yrs. experience. I have written so many blogs and also have sound knowledge in software testing.