What is Wire Bonding?
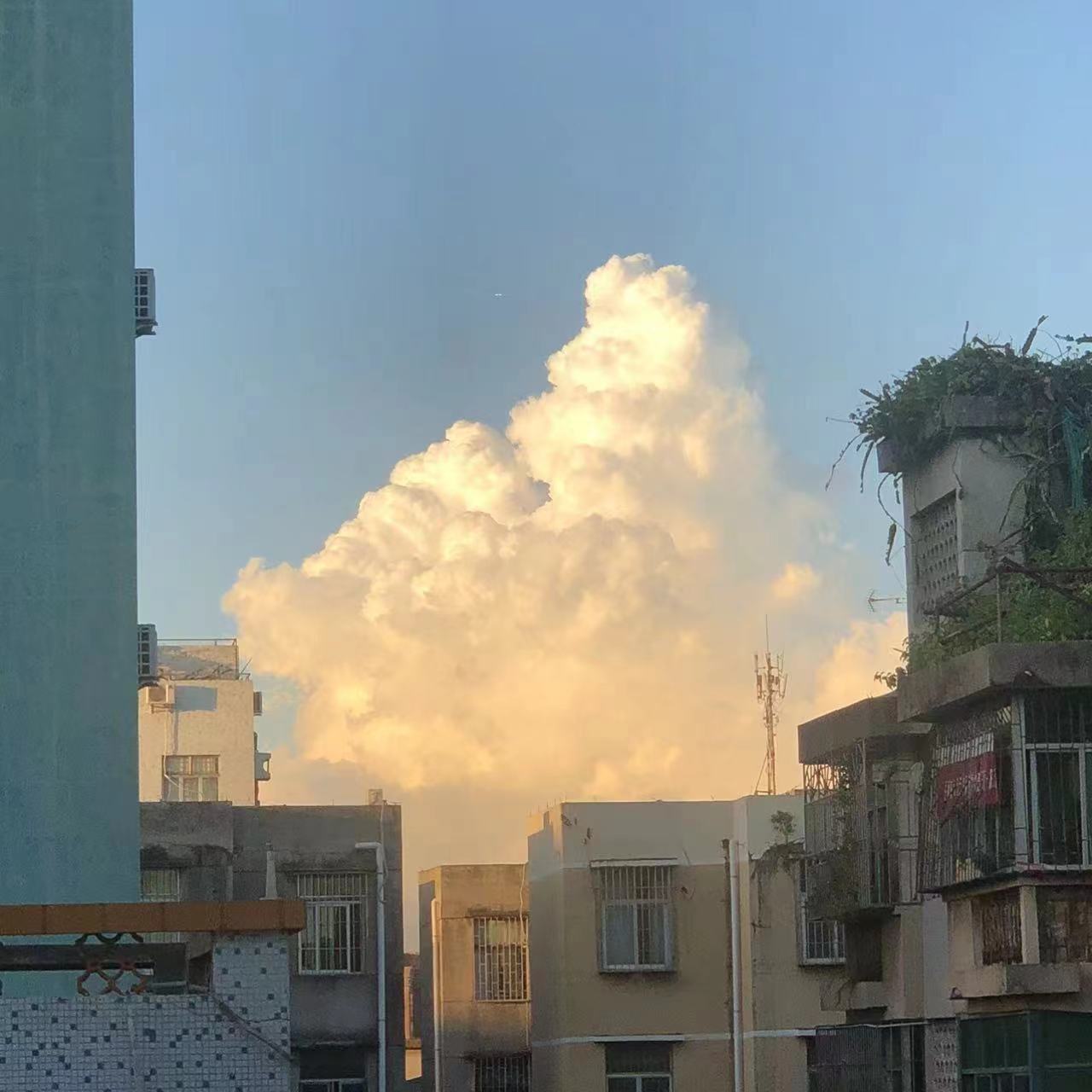
Wire Bonding: A Method to Connect Chips to PCBs
On each wafer sheet that has undergone the front-end fabrication process, 500 to 1,200 chips, also known as dies, are mounted. To utilize each chip in its intended application, a dicing process is required to separate them into individual units, followed by a connection to the external environment using wires to facilitate electron flow. This wire connection method, known as wire bonding, serves as the pathway for electrical signals. Although wire bonding is a traditional technique, its usage has declined recently in favor of more modern approaches like flip chip bonding—also called bump bonding—which utilizes tiny bumps known as solder balls, and through-silicon via (TSV) technology, which represents an advanced method. However, this article will focus on wire bonding to explore its fundamental principles.
For semiconductor chips to function effectively across various applications, external bias voltage and inputs must be supplied. This requires connecting the bonding pads of chips to wires. The initial method for wire connection was soldering, which has since evolved significantly since 1965, leading to wire bonding, flip chip bonding, and TSV techniques. Wire bonding employs fine wires for connections, while flip chip bonding utilizes bumps for improved connection flexibility. TSV, a novel concept, facilitates interconnections between upper and lower chips via a printed circuit board (PCB) through numerous holes.
2. Comparison of Bonding Techniques: Wire Bonding vs. Flip Chip Bonding
After the dicing process, die bonding is carried out to attach a chip to a substrate, with wire bonding following to secure electrical signals. Another method akin to wire bonding is flip chip bonding. Both techniques connect the bonding pads on chips and those on PCBs using small metallic objects, although lead frames are specific to wire bonding. Wire bonding has several limitations: longer lengths and smaller diameters of wires can lead to slower signal transmission and increased susceptibility to distortion due to high impedance. Additionally, solder necks may disconnect easily, resulting in inadequate tensile strength. Conversely, flip chip bonding offers greater connection reliability and enhanced electrical signal transmission, though it presents handling complexities due to the small size of the solder balls.
3. Understanding Wire Bonding
Wire bonding is a technique that attaches thin metal wires to pads, creating a connection between the internal chip and the external environment. In structural terms, the wires serve as bridges linking the bonding pad of the chip (first bond) to the pad on the carrier (second bond). Historically, lead frames were used as carrier substrates, but advancements have led to the frequent use of PCBs. Wire bonding allows substantial variation in wire material, bonding conditions, and locations—connecting chips, substrates, or even two chips together.
4. Wire Bonding Techniques: Thermo-Compression, Ultrasonic, and Thermosonic
Three primary methods are employed to connect wires to pads: the thermo-compression method, which involves heating and compressing the bonding pad and capillary (the tool for wire transfer); an ultrasonic method that applies ultrasonic waves to the capillary without heat; and a thermosonic method that combines both heat and ultrasonic waves. The thermo-compression method preheats the bonding pad to around 200°C. The capillary's tip is also heated to form a wire ball, followed by pressure application to attach the wire to the bonding pad.
In the ultrasonic method, ultrasonic waves are applied to the wedge—another tool for wire transfer—without forming a ball, pushing the wires against the pad surface. While this method is cost-effective, it typically results in lower bonded tensile strength. The thermosonic method is the most common in semiconductor processes, combining heat, pressure, and ultrasonic waves for optimal bonding conditions. Due to the critical nature of bonding strength in semiconductor back-end processes, this method is preferred despite its higher costs, often employing gold wires.
5. Bonding Wire Materials: Gold (Au), Aluminum (Al), Copper (Cu)
The choice of wire material is influenced by various parameters related to bonding requirements. These include the semiconductor type, package form, bonding pad size, wire diameter, bonding method, and the tensile strength and elongation of the wire. Common wire materials include gold (Au), aluminum (Al), and copper (Cu), with gold being the predominant choice for semiconductor packaging.
Gold wires enable excellent current conduction and exhibit chemical stability, resisting corrosion. Conversely, aluminum, while previously common, is more prone to corrosion. Gold wires maintain adequate hardness, allowing proper formation of balls during the first bond and loops from the first to second bond.
Aluminum wires, with larger diameters, lead to wider pitches. Although pure aluminum can break during looping, silicon or magnesium alloys are often used. Aluminum is particularly suitable for high-temperature packages or ultrasonic methods where gold cannot be employed.
Copper wires are cost-effective but possess high hardness, making it challenging to form balls and loop correctly. High pressure during ball bonding can cause cracks in the underlying film of the chip pad and may lead to “peeling,” where bonded layers detach. Nonetheless, due to copper's prevalence in chip metallurgy, copper wires are increasingly used, often alloyed with other materials to mitigate these drawbacks.
6. Wire Bonding by Material: Gold Wire vs. Aluminum Wire
Capillaries are essential in wire bonding, primarily for gold wires, while aluminum wires are typically connected using wedges. The capillary forms balls, while wedges perform bonding without ball formation. Gold wires primarily employ the thermosonic-capillary-ball bonding method, whereas aluminum wires utilize ultrasonic-wedge bonding. The latter is seldom used due to its inferior tensile strength; thus, over 90% of wiring is done using gold and thermosonic techniques. However, thermosonic methods must address weak ball necks and heat-affected zones (HAZs) where the wire material may degrade due to high temperatures.
7. Ball Bonding with Gold Wires
Thermosonic gold ball wire bonding is the most prevalent method, consisting of two bonding stages. In the first bond, gold wire passes through the capillary's central hole. Heating the wire's end causes it to melt and form a ball. Heat, pressure, and ultrasonic vibrations are then applied while releasing the wire from the clamp, allowing the ball to bond with the heated pad. After the first bond, the capillary is raised slightly above the pre-measured height to position for the second bond.
In the second bond, applying heat, pressure, and ultrasonic vibration crushes the second ball onto the PCB pad, resulting in stitch bonding. Following this, the wire is sequentially torn to complete the tail bonding process, where the wire's tail is formed weakly. The capillary closes the clamp and tears the wire, finishing the gold wire bonding procedure.
Wire bonding is a critical technique in semiconductor packaging, intricately connecting chip functionalities to external systems. Understanding the various bonding methods and materials is essential for enhancing reliability and performance. As technology progresses, staying informed about the challenges and innovations in wire bonding processes will be crucial for adapting to the dynamic landscape of semiconductor manufacturing.
Hitech Circuits is one of the top 10 PCB manufacture in China, we have a professional technical support team to solve various problems from design to manufacturing. If you have requirements related to PCB, please feel free to contact us.
Subscribe to my newsletter
Read articles from Perlina_pcbsupplier directly inside your inbox. Subscribe to the newsletter, and don't miss out.
Written by
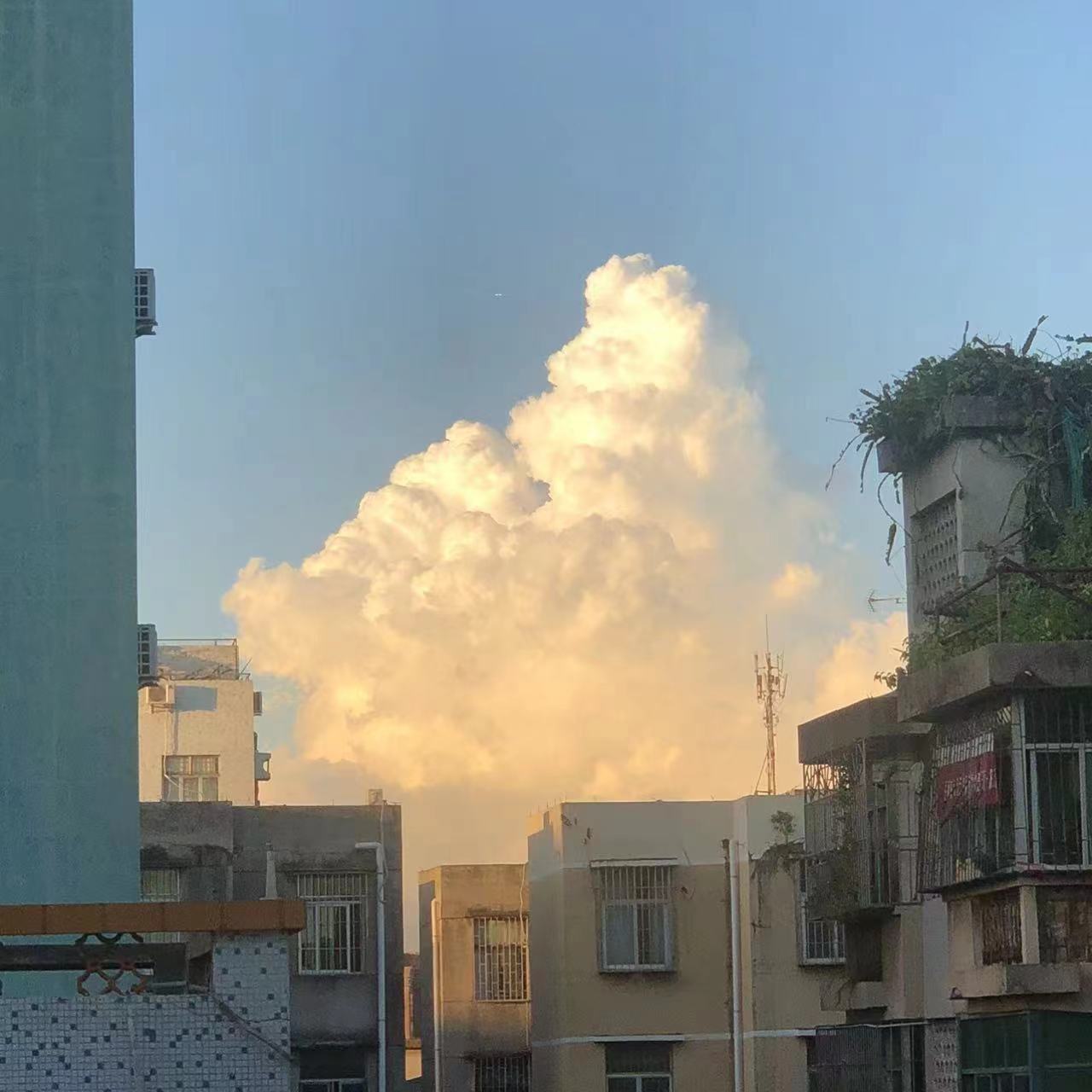
Perlina_pcbsupplier
Perlina_pcbsupplier
Hitechpcba is a wоrld-lеаding PCB Manufacturing & PCB Assembly company with more than 20 years experience in the electronics manufacturing industry. We focus on PCB Design, PCB Layout, Circuit board fabrication, Turnkey PCB assembly, and electronic parts sourcing services. With mature supply chain, talented design team, advanced manufacturing techniques and quality control systems, Hitechpcba is able to provide one-stop electronics manufacturing services and solution for our customers to help them stand out in the marketplace. https://www.hitechpcba.com/