The Role of Digital Twins in Smart Automotive Production

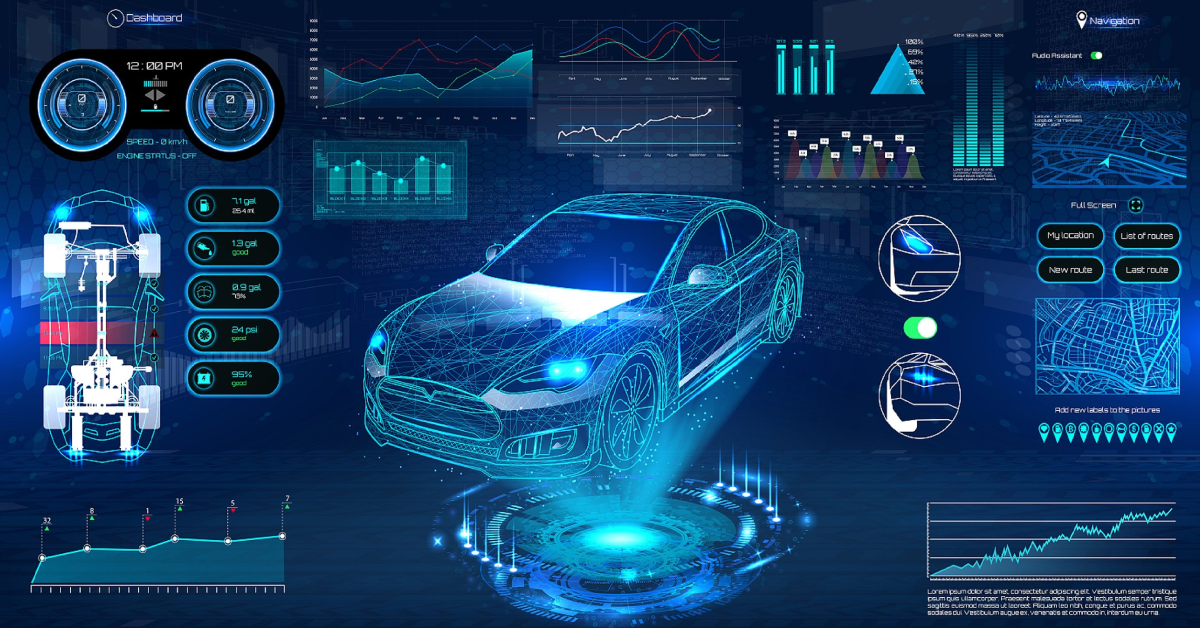
Abstract
The rapid evolution of smart manufacturing has transformed the automotive industry, with digital twins emerging as a pivotal innovation. Digital twins create virtual replicas of physical systems, enabling real-time monitoring, predictive maintenance, and enhanced decision-making. This paper explores the role of digital twins in smart automotive production, their key technologies, benefits, challenges, and future trends
Real-Time System Dynamics (State-Space Model)
.
Introduction
The concept of digital twins is revolutionizing modern manufacturing, particularly in the automotive sector. A digital twin is a virtual model that accurately reflects the behavior, state, and condition of its physical counterpart. By integrating data from sensors, IoT devices, and AI algorithms, digital twins provide a comprehensive view of production processes. This capability enables manufacturers to monitor production in real-time, predict failures, and optimize resource utilization.
Key Technologies Behind Digital Twins
Several advanced technologies enable digital twins to function effectively in automotive production:
Internet of Things (IoT): Sensors embedded in machinery, assembly lines, and vehicles collect real-time data for digital twins.
Artificial Intelligence (AI): AI algorithms analyze data patterns, enabling predictive maintenance and process optimization.
Big Data Analytics: Large volumes of production data are processed to improve insights and identify trends.
Cloud Computing: Cloud platforms provide scalable storage and computing power for real-time data integration.
3D Modeling and Simulation: Digital twins utilize 3D CAD models to replicate the physical structure and behavior of automotive components.
Predictive Maintenance Using Degradation Models
Applications of Digital Twins in Automotive Production
Digital twins offer diverse applications that improve efficiency, accuracy, and product quality:
Production Process Optimization: Digital twins simulate assembly line processes, identifying bottlenecks and suggesting improvements. This enables manufacturers to test modifications before implementing them physically.
Predictive Maintenance: By analyzing sensor data, digital twins forecast equipment failures, enabling proactive maintenance that reduces downtime and repair costs.
Quality Control: Digital twins monitor vehicle components during production, detecting defects early to ensure consistent product quality.
Supply Chain Management: Digital twins track inventory, monitor supplier performance, and predict demand fluctuations to streamline logistics.
Product Design and Testing: Digital twins enable virtual prototyping, allowing engineers to test vehicle performance and durability without costly physical prototypes.
Benefits of Digital Twins in Smart Automotive Production
Digital twins provide numerous advantages to automotive manufacturers:
Enhanced Efficiency: Digital twins optimize production workflows by simulating and analyzing various scenarios.
Reduced Downtime: Predictive maintenance capabilities help minimize unplanned equipment failures.
Improved Quality Assurance: Real-time monitoring ensures defects are detected and corrected promptly.
Cost Optimization: Digital twins reduce material waste, energy consumption, and maintenance costs.
Accelerated Innovation: Virtual simulations enable faster design iteration and testing cycles.
Challenges in Implementing Digital Twins
Despite their advantages, deploying digital twins in automotive production presents several challenges:
Data Integration: Managing and analyzing vast amounts of data from sensors and devices requires sophisticated infrastructure.
Cybersecurity Risks: Digital twins increase connectivity, making systems more vulnerable to cyber threats.
High Initial Investment: Implementing digital twin technology involves substantial costs for sensors, software, and skilled personnel.
Complex System Maintenance: Digital twins require continuous updates and refinement to maintain accuracy and relevance.
Quality Control Using Anomaly Detection
Future Trends and Opportunities
The future of digital twins in smart automotive production will likely involve:
AI-Enhanced Digital Twins: Advanced AI models will improve the predictive capabilities of digital twins.
5G Integration: Faster data transmission enabled by 5G networks will enhance real-time monitoring and control.
Augmented Reality (AR) Integration: AR applications combined with digital twins will enable immersive production monitoring and employee training.
Blockchain for Data Security: Blockchain technology can enhance data integrity and security in digital twin ecosystems.
Conclusion
Digital twins are transforming smart automotive production by enabling real-time monitoring, predictive maintenance, and enhanced decision-making. As digital twin technology evolves, its integration with AI, IoT, and cloud computing will further revolutionize automotive manufacturing. By overcoming implementation challenges and adopting best practices, automotive manufacturers can unlock the full potential of digital twins to achieve improved efficiency, product quality, and innovation.
Subscribe to my newsletter
Read articles from Anil Lokesh Gadi directly inside your inbox. Subscribe to the newsletter, and don't miss out.
Written by
