AI and Robotics in Railway Component Manufacturing

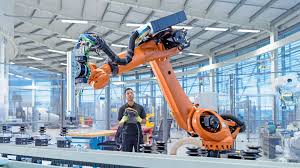
Introduction
The integration of Artificial Intelligence (AI) and robotics has significantly transformed railway component manufacturing. As railway systems evolve to meet modern demands for efficiency, safety, and sustainability, AI-driven systems and robotic technologies have emerged as vital tools. These innovations enhance production precision, streamline manufacturing processes, and improve quality control. This research explores the role of AI and robotics in railway component manufacturing, focusing on their applications, benefits, challenges, and future trends.
The Role of AI in Railway Component Manufacturing
AI plays a crucial role in enhancing decision-making, process optimization, and quality assurance in railway manufacturing. Through machine learning algorithms, data analytics, and predictive modeling, AI systems improve production efficiency and ensure product consistency.
Key Applications of AI
Predictive Maintenance:
- AI systems analyze data from sensors embedded in manufacturing equipment to predict potential failures. This proactive approach minimizes downtime, reduces maintenance costs, and ensures uninterrupted production.
Process Optimization:
- AI-driven algorithms identify inefficiencies in manufacturing processes, recommending adjustments to improve throughput and resource utilization. These insights enable manufacturers to optimize production schedules and material usage.
Defect Detection and Quality Control:
- Machine learning models trained on visual inspection data detect defects in railway components such as cracks, misalignments, or surface imperfections. Automated quality control systems ensure precise assessments with minimal human oversight.
Supply Chain Management:
- AI solutions forecast demand patterns, enabling manufacturers to manage inventory efficiently. By predicting material shortages or excesses, AI systems ensure uninterrupted production.
The Role of Robotics in Railway Component Manufacturing
Robotic systems perform complex and repetitive tasks with high precision and consistency. Robots in railway manufacturing improve welding accuracy, component assembly, and material handling while reducing the risk of human error.
Key Applications of Robotics
Welding and Metal Joining:
- Robotic welding systems perform intricate welds with precision, ensuring structural integrity in railway components such as bogies, frames, and undercarriages. These robots minimize defects by maintaining consistent welding parameters.
Material Handling and Logistics:
- Automated guided vehicles (AGVs) transport heavy materials across manufacturing plants, reducing labor-intensive tasks and improving workflow efficiency.
Assembly Line Automation:
- Robotic arms equipped with sensors perform repetitive assembly tasks such as bolting, drilling, and fitting with exceptional accuracy, ensuring consistent quality.
Surface Treatment and Finishing:
- Robotic systems apply coatings, paints, and protective layers with uniform precision, enhancing the durability and visual appeal of railway components.
Benefits of AI and Robotics in Railway Component Manufacturing
Improved Precision:
- AI-driven systems analyze vast amounts of data to ensure exact measurements, minimizing errors during manufacturing. Robotic tools follow predefined patterns for precise cuts, welds, and assemblies.
Enhanced Efficiency:
- Automation streamlines repetitive tasks, accelerating production cycles. Robotic systems operate continuously, reducing delays and improving throughput.
Cost Reduction:
- By minimizing errors, reducing material waste, and optimizing resource utilization, AI and robotics lower overall production costs.
Increased Safety:
- Robots perform hazardous tasks such as heavy lifting, welding, and exposure to toxic substances, reducing the risk of workplace accidents.
Consistent Quality:
- AI-based quality control systems detect defects in real-time, ensuring uniform product quality and minimizing recalls.
Challenges in Implementing AI and Robotics
High Initial Investment:
- The adoption of AI and robotics requires substantial investment in machinery, software, and staff training.
Integration Complexity:
- Integrating AI and robotic systems with legacy manufacturing equipment can be complex and require extensive customization.
Data Security Concerns:
- AI systems rely on data sharing, raising concerns about intellectual property protection and cybersecurity threats.
Skilled Workforce Requirement:
- Employees must be trained to manage, maintain, and troubleshoot AI and robotic systems to ensure optimal performance.
Case Studies
Siemens Mobility:
- Siemens has integrated AI-driven predictive maintenance and robotic welding systems in their manufacturing plants. These technologies have improved production timelines, reduced errors, and enhanced component durability.
Alstom:
- Alstom leverages AI in its quality inspection process, using machine vision systems to identify microscopic defects in railway components, ensuring precise manufacturing standards.
CRRC Corporation:
- CRRC has employed robotic arms and automated material handling systems to streamline railway component assembly, enhancing efficiency and reducing manual labor requirements.
Future Trends in AI and Robotics for Railway Manufacturing
Autonomous Robotic Systems:
- Future developments will see more autonomous robots capable of adapting to dynamic manufacturing environments and performing multiple tasks without human intervention.
AI-Driven Digital Twins:
- Digital twin technology, powered by AI, will enable manufacturers to create virtual models of railway components, simulating performance and identifying potential design flaws before production.
Collaborative Robots (Cobots):
- Cobots will increasingly work alongside human operators to improve flexibility and efficiency in complex manufacturing tasks.
Enhanced Data Analytics:
AI systems will continue to refine data analysis capabilities, enabling predictive maintenance models and optimizing energy consumption in manufacturing plants.
Conclusion
AI and robotics have revolutionized railway component manufacturing, enhancing precision, efficiency, and quality control. By integrating these advanced technologies, manufacturers can minimize errors, improve productivity, and reduce costs. As AI-driven innovations such as digital twins and autonomous robots continue to evolve, the railway manufacturing industry will benefit from greater automation, increased safety, and improved sustainability. Embracing AI and robotics is essential for meeting the growing demands of modern railway networks and ensuring long-term operational excellence.
Subscribe to my newsletter
Read articles from Rama Chandra Rao Nampalli directly inside your inbox. Subscribe to the newsletter, and don't miss out.
Written by
