Smart Factories in Semiconductor Manufacturing: Industry 4.0 Applications

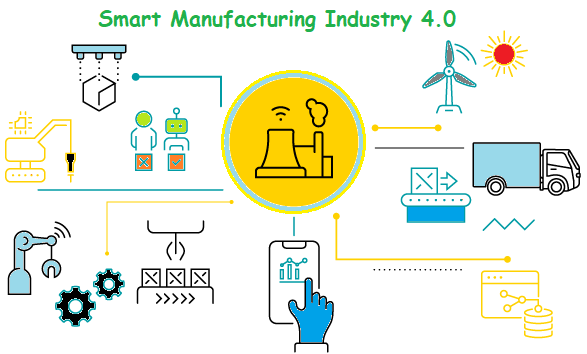
Abstract
The semiconductor industry is undergoing a major transformation with the integration of Industry 4.0 technologies. Smart factories leverage artificial intelligence (AI), machine learning (ML), the Internet of Things (IoT), cloud computing, and automation to enhance efficiency, reduce defects, and optimize supply chains. This paper explores the key applications of Industry 4.0 in semiconductor manufacturing, including predictive maintenance, digital twins, and advanced process control.
1. Introduction
Semiconductor manufacturing is one of the most complex and precise industries, requiring extreme accuracy at the nanoscale level. Traditional manufacturing processes are facing challenges related to increasing design complexity, yield improvement, and cost reduction. The emergence of Industry 4.0 has enabled the transition toward smart factories, where connected systems and data-driven decision-making improve efficiency and productivity.
Industry 4.0 technologies such as AI, ML, IoT, robotics, cloud computing, and big data analytics are being integrated into semiconductor fabrication plants (fabs) to optimize production and minimize defects. This paper highlights the key applications of Industry 4.0 in semiconductor smart factories.
2. Key Industry 4.0 Applications in Smart Semiconductor Factories
2.1 Predictive Maintenance with AI and IoT
Equipment failures in semiconductor fabrication can lead to high costs and production delays. Predictive maintenance (PdM) uses AI and IoT to monitor equipment health and predict failures before they occur.
IoT sensors collect real-time data on machine vibrations, temperature, pressure, and performance.
Machine learning algorithms analyze historical data to predict failures and recommend maintenance actions.
Cloud-based dashboards allow factory managers to monitor equipment health remotely.
This reduces unplanned downtime, improves tool utilization, and lowers maintenance costs.
2.2 Digital Twins for Process Optimization
A digital twin is a virtual replica of a physical manufacturing system that simulates real-world conditions. In semiconductor fabs, digital twins help:
Optimize production parameters by running simulations before making changes in the real process.
Improve yield by identifying defects and process inefficiencies.
Enhance supply chain management by predicting material shortages and optimizing logistics.
For example, chipmakers like Intel and TSMC use digital twins to simulate wafer fabrication processes and fine-tune them in real-time.
2.3 AI-Powered Process Control and Yield Improvement
Yield enhancement is critical in semiconductor manufacturing, where even a tiny defect can make a chip unusable. Industry 4.0 technologies help improve yield by:
Automating defect detection: AI-powered computer vision systems inspect wafers for microscopic defects.
Real-time process adjustments: ML algorithms analyze data from fabrication processes and adjust parameters (e.g., temperature, pressure, deposition rates) to minimize defects.
Advanced metrology tools: Smart sensors track variations in wafer quality, helping reduce defect density.
By integrating AI into fabrication processes, fabs can improve production efficiency and reduce material waste.
2.4 Robotics and Automation in Smart Factories
Automation plays a crucial role in Industry 4.0-driven semiconductor manufacturing. Smart factories utilize:
Autonomous mobile robots (AMRs) for material handling and transportation of wafers.
Robotic arms for high-precision wafer processing, reducing human-induced errors.
Automated guided vehicles (AGVs) to transport semiconductor components between production areas.
Robotics helps maintain a clean environment, minimizes contamination, and enhances overall efficiency.
2.5 Edge Computing and Cloud Integration
The massive amount of data generated in semiconductor fabs requires robust processing and storage solutions. Edge computing and cloud technologies enable:
Faster decision-making by processing critical data at the edge, reducing latency.
Scalability by integrating cloud-based analytics for predictive modeling.
Remote monitoring and control of fab operations across different locations.
For instance, AWS and Microsoft Azure provide cloud-based AI tools that analyze semiconductor production data in real time.
3. Challenges in Implementing Smart Factories
While Industry 4.0 offers significant benefits, there are challenges in adopting smart factory technologies:
High implementation costs: Upgrading legacy semiconductor fabs to Industry 4.0 standards requires significant investment.
Data security concerns: Cloud-connected fabs are vulnerable to cyber threats and intellectual property theft.
Skilled workforce shortage: The industry needs experts in AI, data science, and automation for effective implementation.
System integration issues: Existing semiconductor manufacturing systems must be integrated with Industry 4.0 technologies without disrupting production.
Despite these challenges, continuous advancements in AI, cloud computing, and automation are driving the semiconductor industry toward fully digitalized, intelligent smart factories.
4. Conclusion
Industry 4.0 is transforming semiconductor manufacturing by enhancing productivity, reducing defects, and optimizing resource utilization. Key applications such as predictive maintenance, digital twins, AI-driven process control, robotics, and cloud computing are revolutionizing fabs and improving semiconductor yield. While challenges exist, companies that adopt smart factory technologies will gain a competitive edge in the rapidly evolving semiconductor landscape.
The future of semiconductor manufacturing lies in fully automated, AI-driven smart factories, enabling faster, more efficient, and defect-free chip production for next-generation technologies such as 5G, AI, autonomous vehicles, and quantum computing.
Subscribe to my newsletter
Read articles from Preethish Nanan Botlagunta directly inside your inbox. Subscribe to the newsletter, and don't miss out.
Written by
