Examples of AI Pilot and Scaling Reports for Manufacturing

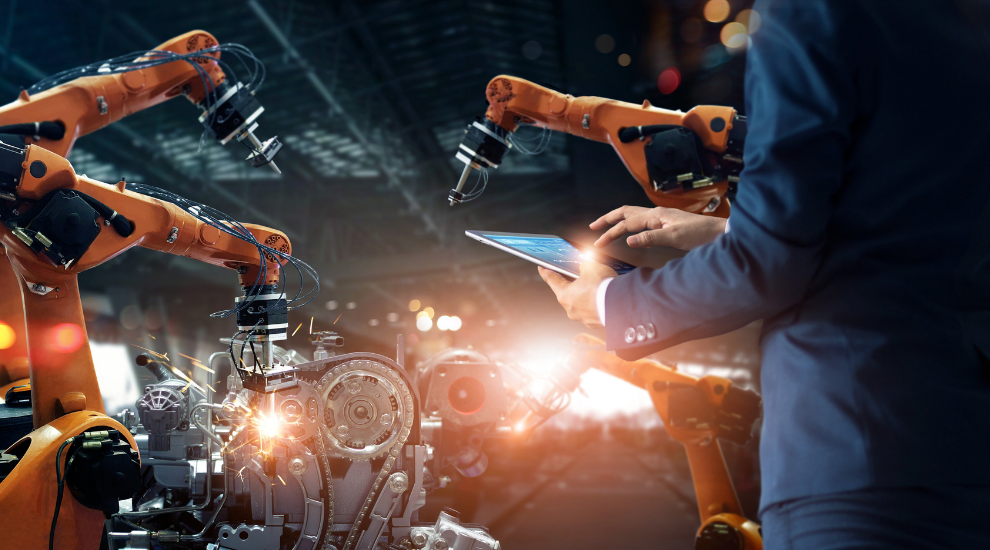
Successfully integrating AI in manufacturing requires a structured evaluation of pilot projects, seamless system integration, and a clear return on investment (ROI) assessment before full-scale deployment. Below are detailed examples of three critical reports used in AI implementation.
1. AI Pilot Performance Report
Objective
Evaluate the effectiveness of an AI pilot project, measure performance against key metrics, and determine the feasibility of scaling.
Pilot Project Summary
Company: XYZ Manufacturing
AI Solution: Predictive Maintenance for CNC Machines
Pilot Start Date: January 2024
Pilot End Date: April 2024
Pilot Location: Midwest Production Facility
Primary Goal: Reduce unplanned machine downtime by 30% using AI-driven failure prediction.
Performance Metrics
Key Findings
AI successfully reduced downtime by 59%, surpassing the initial 30% goal.
Maintenance costs were cut by $70,000 per quarter, leading to an annualized savings of $280,000.
Operators initially reported hesitancy in trusting AI-driven alerts, requiring additional training.
False positives were low (5%), indicating a well-calibrated AI model.
Challenges & Adjustments
Some older machines lacked IoT sensors, requiring manual data entry workarounds.
AI recommendations for maintenance scheduling needed refinement to align with operator preferences.
Conclusion & Recommendations
Proceed with full-scale deployment across additional manufacturing lines.
Expand AI integration to legacy machines by retrofitting IoT sensors.
Conduct additional operator training to build trust in AI-generated recommendations.
2. System Integration Plan
Objective
Ensure seamless integration of AI solutions with existing manufacturing systems, minimizing disruption and maximizing efficiency.
Integration Scope
AI System: Predictive Maintenance AI
Existing Systems to Integrate With:
Manufacturing Execution System (MES)
Enterprise Resource Planning (ERP)
IoT Sensor Network
SCADA System
Integration Strategy
Data Flow Diagram
IoT sensors collect real-time machine data.
Data is processed and stored in a cloud-based AI analytics engine.
AI identifies patterns and predicts failures before they occur.
AI alerts are sent to MES for tracking and ERP for maintenance scheduling.
SCADA system displays real-time alerts for machine operators.
Risk Mitigation
Potential Downtime: Schedule integration during planned maintenance periods.
Data Compatibility Issues: Use middleware for data standardization.
Resistance to AI Insights: Conduct change management workshops for staff.
Post-Integration Validation Metrics
AI system successfully integrated with MES, ERP, and SCADA.
AI alerts properly trigger automated maintenance work orders.
AI predictions align with real-world machine failures within a 90% accuracy range.
3. ROI Assessment for Scaling AI Implementation
Objective
Quantify the return on investment (ROI) for scaling AI-driven predictive maintenance across all manufacturing sites.
Scaling Plan
Expand AI deployment to three additional facilities.
Retrofit older machines with IoT sensors to capture more accurate data.
Standardize AI-based maintenance workflows across all sites.
Projected Financial Impact
Implementation Cost Breakdown
ROI Calculation
Annual Savings Across 3 Sites: $1.12M
Total AI Expansion Cost: $750,000
ROI = (Annual Savings / Investment) x 100
ROI = ($1.12M / $750,000) x 100 = 149%
Break-Even Period
- Initial investment recovered within 8 months through maintenance cost savings and productivity gains.
Final Recommendation
Proceed with full AI expansion across all three sites due to strong ROI and short payback period.
Expand AI integration to supply chain logistics for further cost savings.
Continuously optimize AI models with updated real-world data.
Conclusion
AI implementation in manufacturing requires clear performance measurement, structured system integration, and a financial justification for scaling. By following this structured approach:
AI Pilot Performance Report ensures that AI solutions deliver measurable results before full deployment.
System Integration Plan guarantees seamless connectivity between AI and existing IT infrastructure.
ROI Assessment for Scaling justifies the investment and identifies opportunities for additional AI expansion.
For expert guidance on scaling AI in manufacturing, visit valere.io.
Subscribe to my newsletter
Read articles from Valere directly inside your inbox. Subscribe to the newsletter, and don't miss out.
Written by

Valere
Valere
Valere is an award-winning technology innovation & software development company, utilizing emerging technology in Machine Learning (ML) and Generative Artificial Intelligence (GenAI) to enable medium to large enterprises to execute, launch, and scale their vision into something meaningful.