6 Game-Changing Ways AI, IoT, and Automation Are Revolutionizing Manufacturing Production Planning
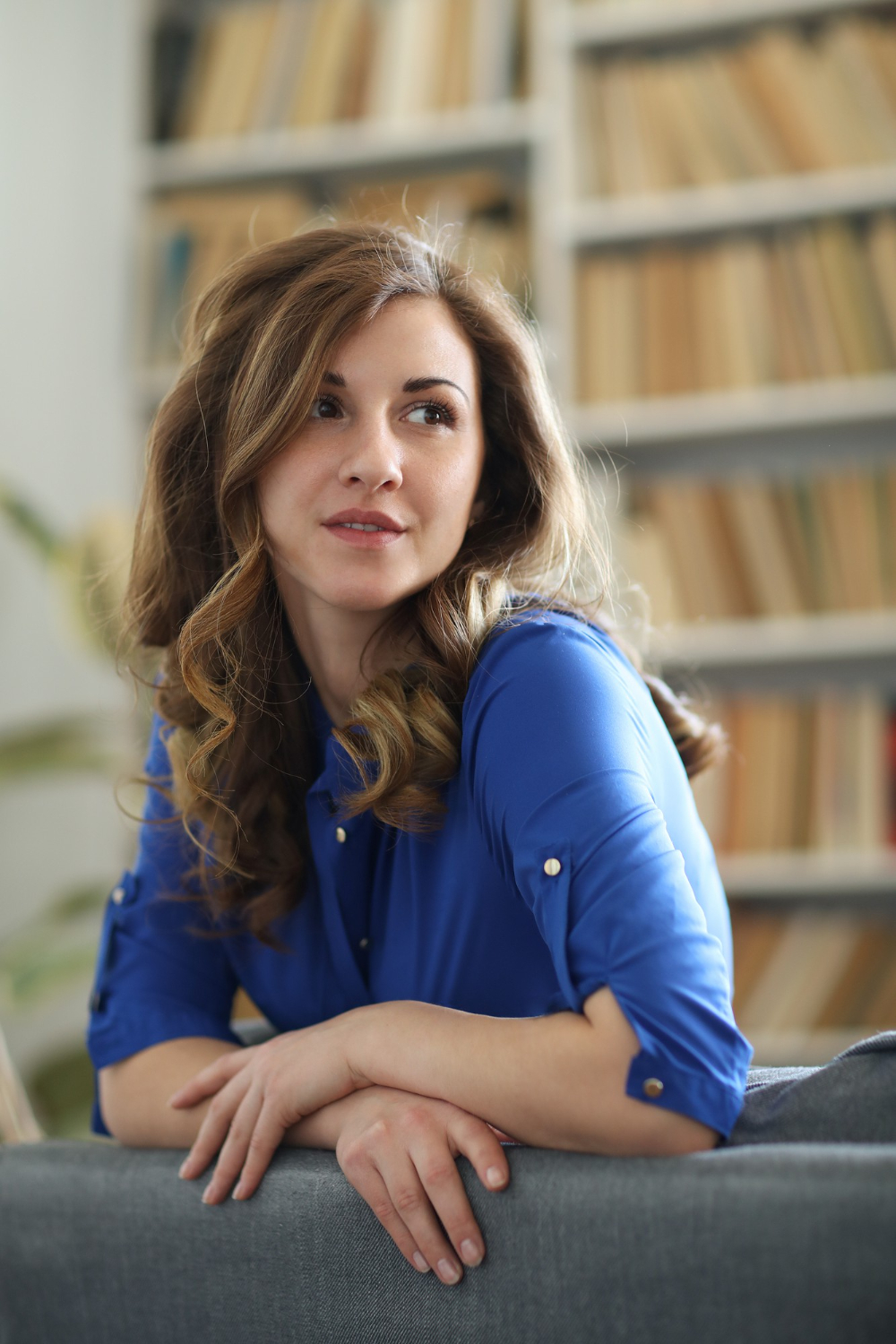
1. Predictive Analytics for Demand Forecasting
In manufacturing, one of the most challenging aspects is ensuring you have the right amount of raw materials, parts, and finished goods at the right time. Too much inventory ties up cash, while too little leads to production delays, stockouts, or missed customer orders. Traditional forecasting methods, which rely on simple averages or past sales data, often miss nuances in market trends or fail to predict sudden spikes in demand.
Artificial Intelligence (AI) and Machine Learning (ML) revolutionize this process by analyzing vast amounts of data, both from historical production records and external sources like market trends, seasonal changes, and even consumer sentiment.
Benefits of Using Predictive Analytics in Manufacturing:
✔ Improved Accuracy
✔ Cost Savings
✔ Better Decision-Making
Role of AQe Digital:
Using artificial intelligence services we implement predictive analytics in manufacturing for accurate demand forecasting which aids in synchronizing the necessary program with market requirements, thus their overall working is improved and cost are reduced.
AI Model Forecast: We apply top of the line machine learning models and deeply analyze the historical sales, customer’s actions towards the product, and the current market tactic to accurately predict what is going to be needed in the future.
Customizable Model: Our proposal is available with regard to the specific requirements of all industries with provided seasons and sudden changes in the market, which include countless primary factors.
Integrated Data System: To achieve precise forecasts and productive production plans, the flow of correct data from various systems is required. Therefore, we combine existing systems ERP, CRM, and others often.
Actionable insights: We provide producers with real-time dashboards and detailed reports, enabling dynamic revision of the production program, which decreases waste and increases customer satisfaction.
2. Dynamic Scheduling and Real-time Decision Making
Dynamic scheduling and real-time decision making are considered a vital part in the wheel of smart manufacturing systems, particularly in the complexity-ridden industries that require efficiency, flexibility, and rapid response to disruptions. AI in manufacturing offers the capability to maintain a continuous analysis of data generated by the system during production so it can instantly readjust schedules, workflows, and allocations of resources in an optimal manner to effectuate efficiency. In such a way, considerations are given to overall optimization of the production process with respect to several rapidly changing parameters, such as machine availability, workforce skills, material availability, and other external factors.
Benefits of Dynamic Scheduling for Manufacturers:
✔ Better Resource Utilization
✔ Minimized Downtime
✔ Faster Time-to-Market
Role of AQe Digital:
Our team develops smart production planning software built on AI and optimization tools that automatically change production schedules based on real-time data to maximize a manufacturer’s efficiency and speed up delivery times, making it more efficient over time and effort.
AI-powered Scheduling: Using AI algorithms, manufacturing production planning software automatically comes up with the best production schedules stemming from the available resources like labor, materials, deadlines, machines, and customer orders.
Adjustments in Real-time: Changes to schedules are instantly updated. Automatic production schedules change according to machine breakdowns, delays, or even demand.
Resource Assignment: Our manufacturing production planning systems guarantee the best assignment of people, machinery, and even raw materials and guarantee the best results by eliminating inefficient tasks and underused resources.
Decreased Lead Times: Meeting deadlines becomes easier and quicker, plus increased order fulfillment equals happiness to customers all while improving the bottom line with the optimized production schedules.
3. Real-Time Monitoring and Data Collection
When equipped with IoT devices, the machinery collects a huge amount of data whenever a particular equipment is in operation; these can be analyzed for predictive failure analysis. For example, sensors can extract data related to temperature, vibration, and other indicators that signal imminent issues. This enables manufacturers to carry out predictive maintenance, thus circumventing expensive breakdowns due to halted production lines.
Benefits of Real-Time Monitoring and Data Collection:
✔ Proactive Issue Resolution
✔ Increased Transparency
✔ Improved Efficiency
Role of AQe Digital:
With IoT-based monitoring solutions, manufacturers keep track of production as events unfold. Our platform offers actionable insights toward predicting issues before they manifest as problems and helps in enhancing productivity.
IoT Integration: Merges real-time data from all of your machines, sensors, and workstations.
Data-Driven Decisions: Advanced algorithms can analyze recorded data and show insights into machine performance, production efficiency, and possible reported problems.
Alerts and Notifications: Immediate and real-time alerts are generated when any deviations, failures, or inefficiencies take place, so you can act before a situation becomes nasty in production.
Better Visualization: You will be given a very user-friendly dashboard where you would see up to the minute where your whole AI in manufacturing process is and make decisions for operations based on that.
4. Predictive Maintenance
Predictive maintenance uses data collected from machines and equipment to predict when maintenance will be required. By using sensors and historical performance data, AI models predict failure points and alert operators to perform maintenance only when necessary, rather than following a fixed schedule.
Benefits of Predictive Maintenance:
✔ Reduced Unplanned Downtime
✔ Lower Maintenance Costs
✔ Better Equipment Reliability
Role of AQe Digital:
With advanced AI in manufacturing technologies using machine learning methods to predict possible failures and proactively schedule maintenance interventions to ensure maximum uptime and long-term reliability of the assets, we offer integrated predictive maintenance solutions for seamless working with the company’s systems.
Condition-Based Monitoring: We use sensors and IoT devices for the continuous health of your machines and analyze enormous data in terms of working conditions — things like temperature, vibration, and pressure to predict failure.
AI-Powered Prediction: Our predictive maintenance systems run on historical data and AI models to warn when maintenance or parts replacement is required, thereby lessening unplanned downtime.
Maintenance Scheduling: We automate the maintenance process by choosing the best time for repair or replacement based on the production schedule to minimize disruption.
Manufacturing Cost Reduction: Performing maintenance of your systems only when it is necessary, rather than using a predetermined set of time, we help you in manufacturing cost reduction on maintenance, increase equipment lifecycle, and allow production to maximize uptime.
Subscribe to my newsletter
Read articles from Sarah R. Weiss directly inside your inbox. Subscribe to the newsletter, and don't miss out.
Written by
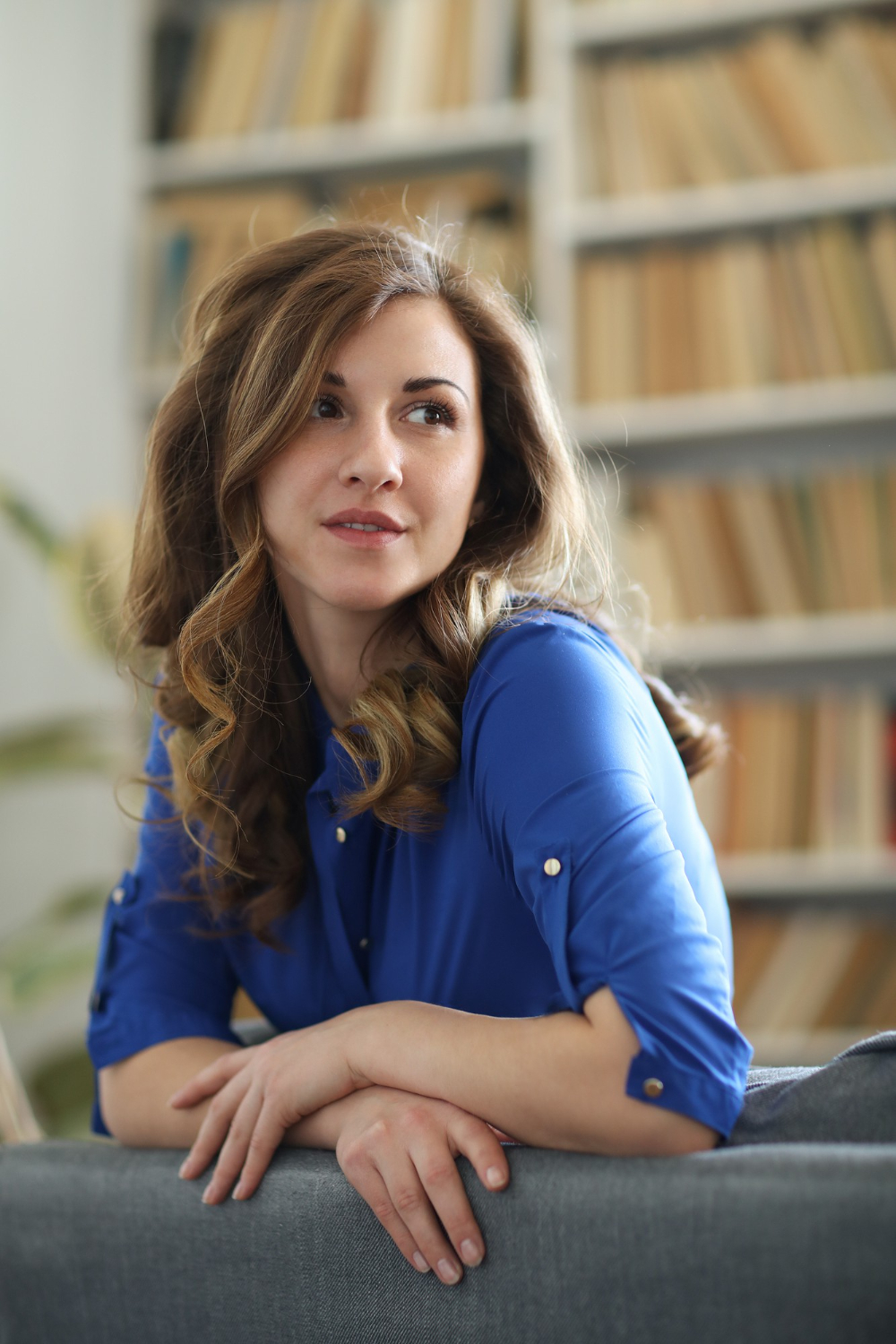
Sarah R. Weiss
Sarah R. Weiss
I share insights on Software Development, Data Science, and Machine Learning services. Let's explore technology together!