Modal Analysis in Abaqus: Ensuring Dynamic Readiness in Automotive Applications đźš—
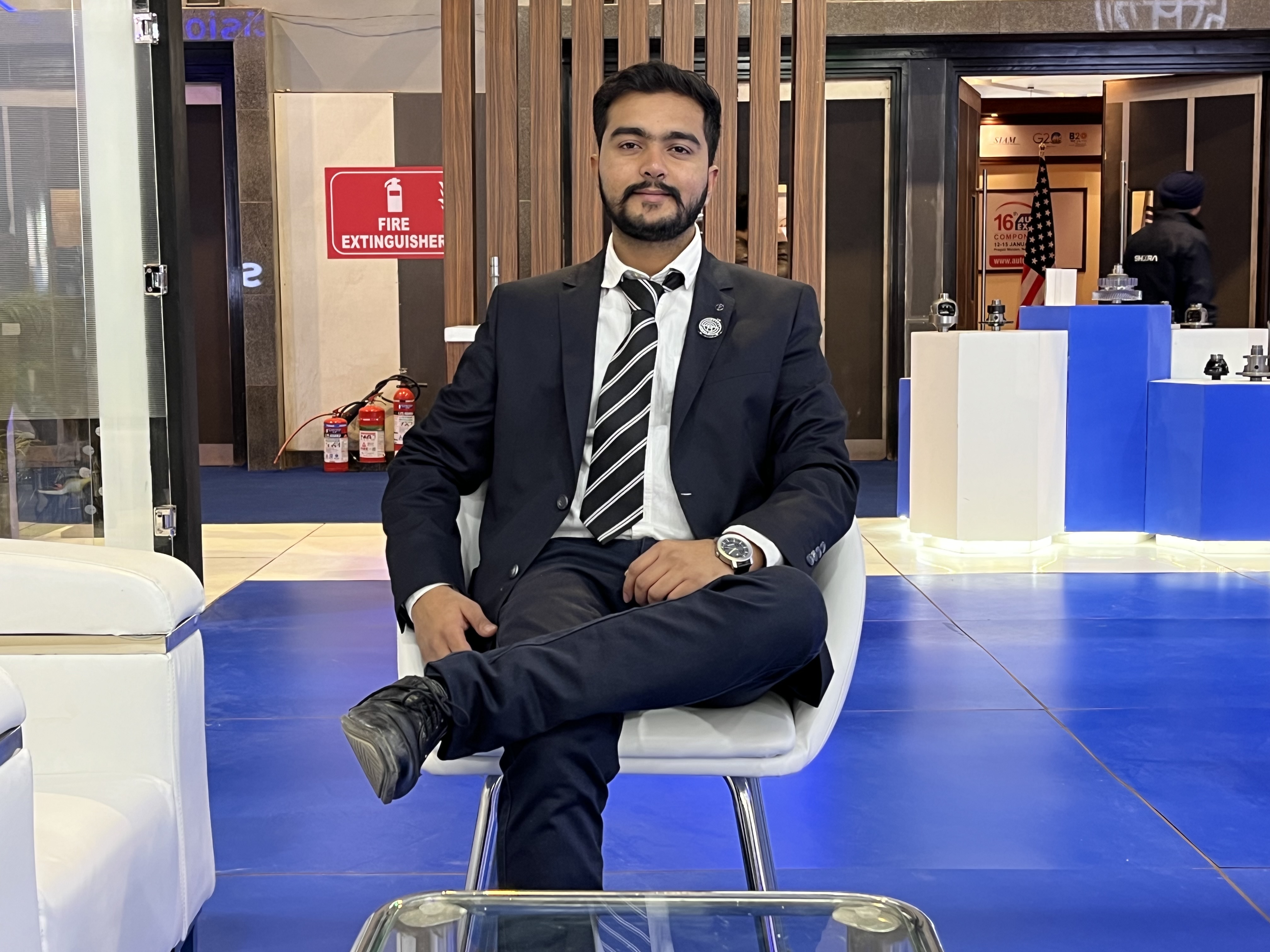

Modal analysis plays a crucial role in the automotive industry to ensure that components like brackets, mounts, suspensions, or dashboards don’t resonate under dynamic loading conditions. Imagine a vehicle’s battery bracket vibrating at the same frequency as the engine or road-induced vibrations—this could lead to fatigue failure, discomfort, or even structural damage. That’s why modal analysis is essential in early design stages.
In this blog, we cover:
Fundamentals of modal analysis in FEM
Role of mode participation factor & effective mass
How to postprocess Abaqus .dat file
Example from shaker table test (SSD)
Visualization of vibration modes
⚙️ FEM Foundation: Solving for Natural Modes
Modal analysis in Abaqus solves the eigenvalue problem:
This solution gives:
Natural frequencies (f=ω/2π)
Mode shapes showing how the structure deforms
These results serve as input to frequency response, PSD (random vibration), modal dynamics, and shock response simulations.
🔹 Modal Participation Factor: What It Tells Us
Mode participation factor indicates how strongly each mode contributes to motion in a given direction. Mathematically, it is calculated as:
$$\text{Participation Factor} = \frac{M_{eff}}{M_{total}}$$
Why It Matters
High participation in a direction = more contribution to motion in that direction
Helps correlate simulation modes with experimental modes (e.g., from shaker table tests)
Helps identify which modes are dominant in the vibration response
📌 Key Insights from Participation Factor Table:
Mode 2 and Mode 3 contribute most to Y-direction motion
Mode 1 and Mode 3 show strong Z-rotation (torsional response)
Other directions (X, Z translations, and X/Y-rotation) are negligible
Signs indicate phase direction (positive = in phase, negative = out of phase)
🔢 Effective Mass: A Measure of Dynamic Influence
Effective mass quantifies how much of the structure’s total mass contributes to motion for a given mode and direction.
Units: kg or ton
Direction-specific (X, Y, Z, and rotations)
The total effective mass for all extracted modes in a direction should be at least 80% of the total structural mass for reliable dynamic results.
📊 Real Example: Bracket under Shaker Table Test
Simulation Setup:
Component: Battery bracket
Material: Viscoelastic + hyperplastic
Analysis Types: Static + Modal + Steady-State Dynamics (SSD)
Pre-stressed modal analysis: Enabled
Base Excitation: Y-direction, 9810 mm/s²
Extracted Frequencies (from .dat file):
Effective Mass Table (from .dat file):
âś… Modal Sufficiency Check
Assume from .dat file that:
Total system mass = 2.0E-04 tones
Total effective mass in Y = 1.84227E-04 tones
Now calculate the ratio of effective mass to total mass which will come around 92%.
✅ Sufficient since it’s >80%
đźš‚ What If It Were Below 80%?
If the effective mass in the loading direction is <80%, it indicates the extracted number of modes is insufficient to capture system dynamics. You must:
Increase the number of extracted modes in your modal step
Re-check the effective mass distribution in the .dat file
This is critical for accurate results in:
Steady-state dynamics
Random response (PSD)
Modal transient
👆 What About Rotations?
If the loading or vibration involves rotations (e.g., gearbox or shaft), verify rotational effective mass (X, Y, Z-rotation)
Make sure total rotational inertia participation is also >80%
đź’Ą Strain Energy Per Mode (Separate Insight)
In some design cases, engineers review strain energy per mode to identify areas of high stress concentration during vibrational loading.
Use Cases:
Identify weak regions or hot spots
Add ribs or local stiffeners
Adjust mass placement
Shift resonance frequency
Additional Insights:
High localized strain energy = potential fatigue risk
Helps target reinforcements to the most vulnerable geometry
Even modes with low effective mass may have high localized strain energy
Important for experimental correlation and failure prevention
âś… Summary & Takeaways
Modal analysis gives the backbone for all linear dynamic simulations
Postprocessing .dat file helps verify modal completeness
Participation factors guide dynamic relevance
Effective mass confirms whether modes are enough
Strain energy offers insights for design optimization
Subscribe to my newsletter
Read articles from Vishal Sharma directly inside your inbox. Subscribe to the newsletter, and don't miss out.
Written by
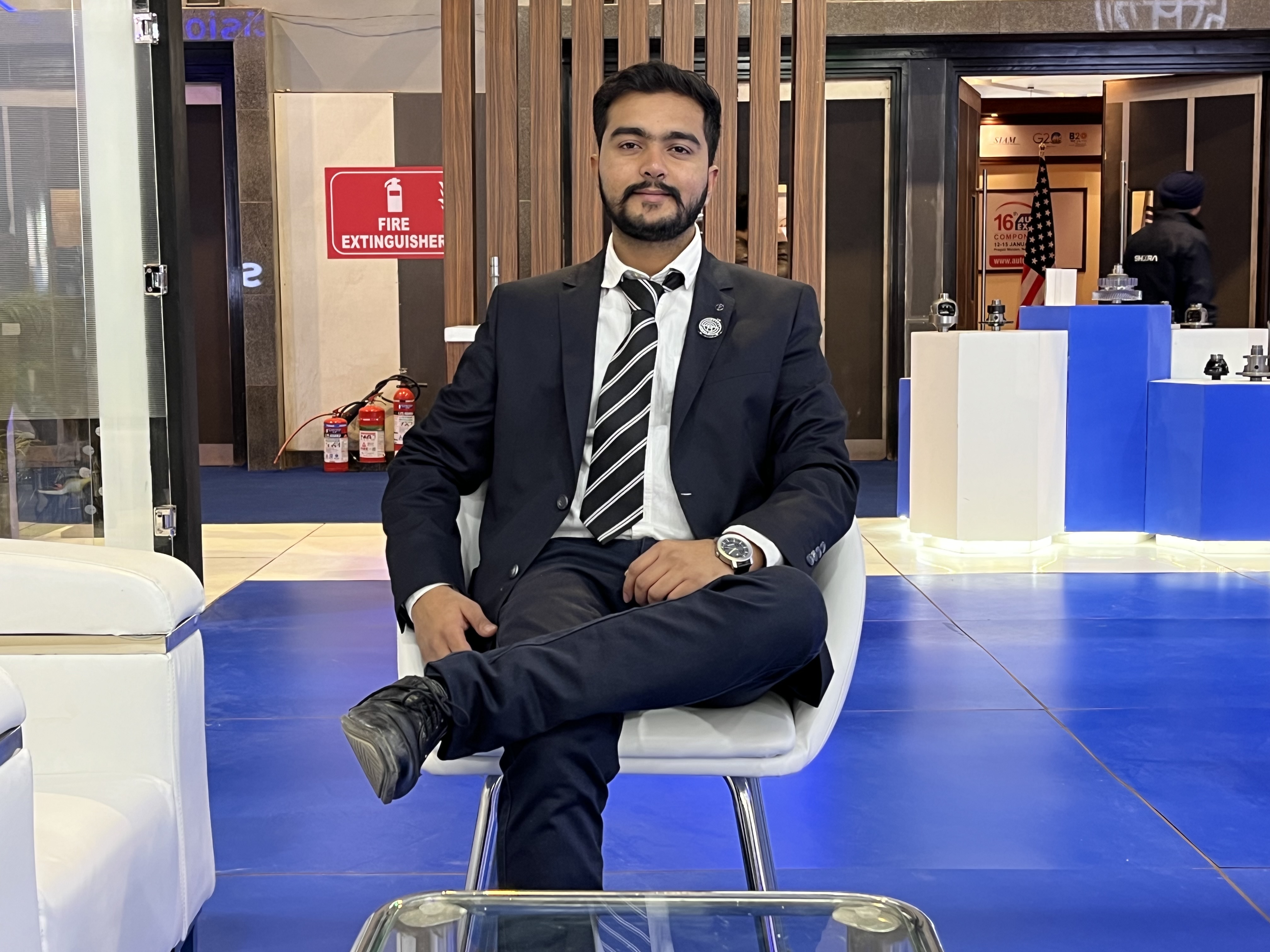
Vishal Sharma
Vishal Sharma
I hold a Master's degree in Mechanical Design from BITS Pilani, a prestigious institution renowned for engineering. Over the years, my journey has taken me through various pivotal roles that enriched my technical expertise and broadened my perspective on the industry. I started with New Product Development, delving deep into the intricate nuances of product creation from scratch. As an FEA engineer, I had the privilege to leverage software tools like Ansys and Hypermesh, allowing me to comprehend the depths of Finite Element Analysis and Computational Fluid Dynamics. Beyond these roles, my passion for teaching led me to become an Associate Instructor at Skill Vertex, and since 2018, I've been actively educating a growing audience on YouTube. My proficiency doesn't just lie in theoretical knowledge but extends to practical software skills as well, with hands-on experience in CATIA, SolidWorks, and Tolerance Stack-Up Analysis. One of my notable achievements includes the research and design of differential assembly and driveline components, which was a testament to my dedication and knack for mechanical designing. But at the core of it all, my true desire is to share. I want to bridge the gap between academia and industry by spreading professional knowledge on FEA, 3D modeling software, and tolerance stack-up analysis. I believe in empowering the next generation of engineers with not just knowledge but the wisdom of experience.